Three-degree-of-freedom parallel serial joint plastic operation robot
A plastic surgery, degree of freedom technology, applied in the direction of surgery, medical science, diagnosis, etc., can solve the problems that affect the accuracy of prosthesis installation and increase the uncertainty of surgery, so as to reduce medical costs, shorten treatment time, and improve surgical safety Effect
- Summary
- Abstract
- Description
- Claims
- Application Information
AI Technical Summary
Problems solved by technology
Method used
Image
Examples
Embodiment Construction
[0027] The following are specific embodiments of the present invention and in conjunction with the accompanying drawings, the technical solutions of the present invention are further described, but the present invention is not limited to these embodiments.
[0028] Such as Figure 1 to Figure 6 As shown, the three-degree-of-freedom serial-parallel hybrid arthroplasty robot includes a workbench 1, on which a vertical mechanism 2 and a horizontal mechanism 4 are arranged, and on the horizontal mechanism 4, a grinding and drilling mechanism 5 is arranged. The workbench 1 includes a combined equipment area and an operation area, a vertical mechanism 2 and a horizontal mechanism 4 are installed in the equipment area, and a grinding and drilling mechanism 5 extends above the operation area through a claw arm.
[0029] There are two horizontal mechanisms 4, which are respectively arranged on both sides of the vertical mechanism 2. The vertical mechanism 2 includes a vertical slide 21...
PUM
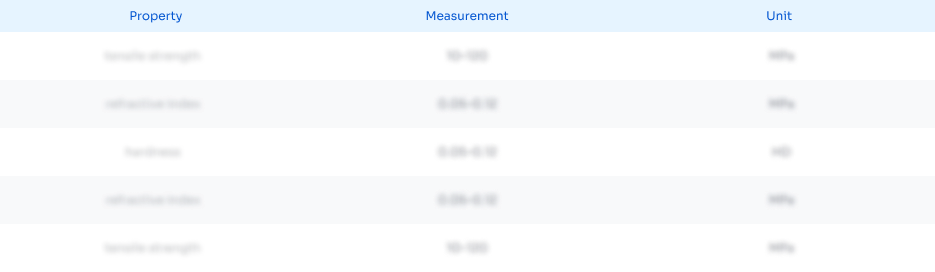
Abstract
Description
Claims
Application Information

- R&D Engineer
- R&D Manager
- IP Professional
- Industry Leading Data Capabilities
- Powerful AI technology
- Patent DNA Extraction
Browse by: Latest US Patents, China's latest patents, Technical Efficacy Thesaurus, Application Domain, Technology Topic, Popular Technical Reports.
© 2024 PatSnap. All rights reserved.Legal|Privacy policy|Modern Slavery Act Transparency Statement|Sitemap|About US| Contact US: help@patsnap.com