Acid-alkali combination method for extraction of aluminum, potassium and gallium from alunite concentrate
An acid-base combination and alumite technology, applied in the direction of improving process efficiency, can solve the problems of equipment corrosion, difficult separation of impurities by acid method, unavailability of acid, etc., and achieve the effect of avoiding separation difficulties.
- Summary
- Abstract
- Description
- Claims
- Application Information
AI Technical Summary
Problems solved by technology
Method used
Image
Examples
Embodiment 1
[0062] Mix 90% of the alunite concentrate with a particle size of less than 200 mesh and 90% of concentrated sulfuric acid. The amount of sulfuric acid added is 1.6 times the mass of the alunite concentrate. Obtain sulfuric acid slaking material. The sulfuric acid slaking material is mixed evenly according to the coal ratio of 8%, and the rapid reduction roasting is carried out at a temperature of 750 ° C for 5 minutes.
[0063] The reduced calcined sand is soaked in water at a temperature of 90°C for 60 minutes and a liquid-to-solid ratio of 2:1, so that potassium enters the water soaking solution and aluminum is enriched in the slag. Potassium sulfate is obtained by evaporating and crystallizing the water immersion solution. The crystallization mother liquor can be returned to add water to leach the new calcined sand.
[0064] Alkali dissolution is carried out on the water leaching residue, and the dissolution conditions are: dissolution temperature 100°C, alkali concentra...
Embodiment 2
[0066] Mix the alunite concentrate with concentrated sulfuric acid, the amount of 93% concentrated sulfuric acid added is 2.2 times the mass of the alunite concentrate, after mixing evenly, the sulfuric acid slaking material is obtained under the conditions of a slaking temperature of 320° C. and a slaking time of 8 hours. The sulfuric acid slaking material is uniformly mixed with coal powder at a coal ratio of 15%, and is subjected to rapid reduction roasting at a temperature of 800°C, and the roasting time is 10 minutes.
[0067] The reduced calcined sand is soaked in water at a temperature of 70°C for 30 minutes and a liquid-solid ratio of 3:1, so that potassium enters the water soaking solution and aluminum is enriched in the slag. Potassium sulfate is obtained by evaporating and crystallizing the water immersion solution. The crystallization mother liquor can be returned to add water to leach the new calcined sand.
[0068] Alkali dissolution is carried out on the water ...
Embodiment 3
[0070] Mix the alunite concentrate with concentrated sulfuric acid, the amount of 95% concentrated sulfuric acid is 1.8 times the mass of the alunite concentrate, after mixing evenly, obtain the sulfuric acid slaking material under the condition of slaking temperature 380°C and slaking time 4h. The sulfuric acid slaking material is passed into the gas in the fluidized roasting furnace, and the rapid reduction roasting is carried out at a temperature of 750 ° C, and the roasting time is 1 min.
[0071]The reduced calcined sand is soaked in water at a temperature of 70°C for 30 minutes and a liquid-solid ratio of 3:1, so that potassium enters the water soaking solution and aluminum is enriched in the slag. Potassium sulfate is obtained by evaporating and crystallizing the water immersion solution. The crystallization mother liquor can be returned to add water to leach the new calcined sand.
[0072] Alkali dissolution is carried out on the water leaching residue, and the dissol...
PUM
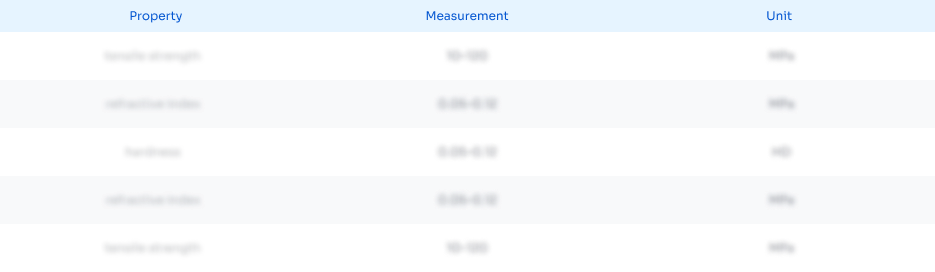
Abstract
Description
Claims
Application Information

- Generate Ideas
- Intellectual Property
- Life Sciences
- Materials
- Tech Scout
- Unparalleled Data Quality
- Higher Quality Content
- 60% Fewer Hallucinations
Browse by: Latest US Patents, China's latest patents, Technical Efficacy Thesaurus, Application Domain, Technology Topic, Popular Technical Reports.
© 2025 PatSnap. All rights reserved.Legal|Privacy policy|Modern Slavery Act Transparency Statement|Sitemap|About US| Contact US: help@patsnap.com