Phosphonitrile fire retardant and preparation method and application thereof
A phosphazene flame retardant and technology for flame retardants are used in the preparation of halogen-free flame retardant composite materials, phosphazene flame retardants and their preparation fields, and can solve the problems of deteriorating mechanical properties of composite materials, narrow melting range and the like, To solve the problem of poor mechanical properties of materials, narrow melting range and good compatibility
- Summary
- Abstract
- Description
- Claims
- Application Information
AI Technical Summary
Problems solved by technology
Method used
Image
Examples
Embodiment 1
[0043] (1) Dissolve 3.00g (0.0086 mol) of hexachlorocyclotriphosphazene and 8.73g (0.086mol) of triethylamine in an inclined three-necked round-bottomed flask (with a condensing device) filled with 100ml of dioxane, and pass Into N 2 protection, put the round-bottomed flask into an oil bath at 80°C, and stir magnetically for 10 minutes to dissolve and mix evenly to obtain a uniform mixture; The dioxane solution of diamine was added dropwise while stirring, and the drop was completed after 2 hours. After the dropwise addition was completed, the reaction was refluxed at 80° C. for 12 hours to obtain a reaction solution;
[0044] (2) Cool the reaction solution to room temperature, let it stand until the layers are separated, filter under reduced pressure to obtain a white precipitate, first rinse with dioxane, then rinse with a large amount of deionized water, and finally put the precipitate into a vacuum oven at 80°C for drying Oven-dried for 12 h, the product hexa-dodecylamino...
Embodiment 2
[0052] (1) Dissolve 3.00g (0.0086 mol) of hexachlorocyclotriphosphazene and 8.73g (0.086mol) of triethylamine in an inclined three-necked round-bottomed flask (with a condensing device) filled with 100ml of dioxane, and pass Into N 2 protection, put the round-bottomed flask into an oil bath at 50°C, and stir magnetically for 8 minutes to dissolve and mix evenly to obtain a uniform mixture; at this time, add 50ml containing 9.546g (0.0516mol) The dioxane solution of diamine was added dropwise while stirring, and the drop was completed after 2 hours. After the dropwise addition was completed, it was refluxed at 80°C for 10 hours to obtain a reaction solution;
[0053] (2) Cool the reaction solution to room temperature, let it stand until the layers are separated, filter under reduced pressure to obtain a white precipitate, first rinse with dioxane, then rinse with a large amount of deionized water, and finally put the precipitate into a vacuum oven at 80°C for drying After oven...
Embodiment 3
[0056] (1) Dissolve 3.00g (0.0086 mol) of hexachlorocyclotriphosphazene in an inclined three-necked round-bottomed flask (with a condensing device) filled with 100ml of dioxane, and inject N 2 protection, put the round-bottomed flask into an oil bath at 80°C, and stir magnetically for 8 minutes to dissolve and mix evenly to obtain a uniform mixture; Diamine and 8.73g (0.086mol) of triethylamine in dioxane solution were added dropwise while stirring, and the drop was completed after 1 hour. After the drop was completed, the solution was refluxed at 75°C for 12 hours to obtain a reaction solution;
[0057] (2) Cool the reaction solution to room temperature, let it stand until the layers are separated, filter under reduced pressure to obtain a white precipitate, first rinse with dioxane, then rinse with a large amount of deionized water, and finally put the precipitate into a vacuum oven at 80°C for drying After oven drying for 12 h, the product hexa-dodecylamino-cyclotriphosphaz...
PUM
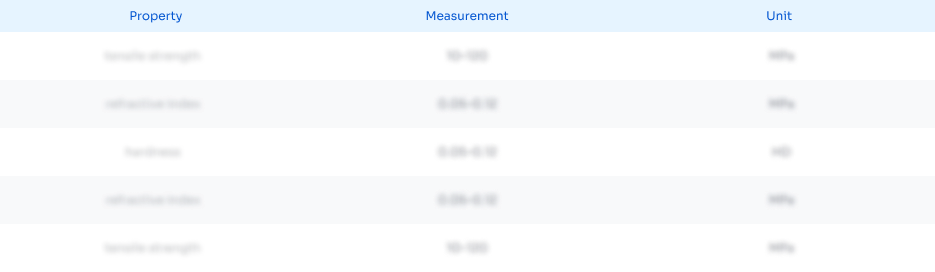
Abstract
Description
Claims
Application Information

- R&D
- Intellectual Property
- Life Sciences
- Materials
- Tech Scout
- Unparalleled Data Quality
- Higher Quality Content
- 60% Fewer Hallucinations
Browse by: Latest US Patents, China's latest patents, Technical Efficacy Thesaurus, Application Domain, Technology Topic, Popular Technical Reports.
© 2025 PatSnap. All rights reserved.Legal|Privacy policy|Modern Slavery Act Transparency Statement|Sitemap|About US| Contact US: help@patsnap.com