Method for forming J-shaped beam structure composite workpiece by open type soft tooling
A composite material and beam structure technology is applied in the field of open flexible tooling to form J-shaped beam structure composite material parts, which can solve the problem of high manufacturing and maintenance costs of metal core molds, excessive thickness of composite material parts, and affecting parts. Internal molding quality and other issues, to achieve the effect of good surface quality, avoid thickness excess, and avoid thermal hysteresis effect
- Summary
- Abstract
- Description
- Claims
- Application Information
AI Technical Summary
Problems solved by technology
Method used
Image
Examples
Embodiment Construction
[0026] The present invention will be further described below in conjunction with the accompanying drawings and specific embodiments.
[0027] Firstly, by means of mechanical manufacturing, a metal dummy that is exactly the same in size as the composite material part, and a soft tooling forming mold with a top plate, a bottom plate and a side baffle are processed. There is an assembly relationship between the parts of the mold, and at the same time Each baffle of the mold will play a certain role in limiting the metal dummy, such as figure 1 shown. The metal dummy can be made of P20 steel, and the soft tooling mold can be made of Q235 steel.
[0028] Use the cavity formed by the metal dummy and the upper and lower baffles to lay soft tooling. The rubber layer is used as the main material of the soft tooling, and the rubber layer is laid in the cavity, and the carbon fiber prepreg is laid in the middle of the rubber layer as a reinforcement layer to improve the overall rigidit...
PUM
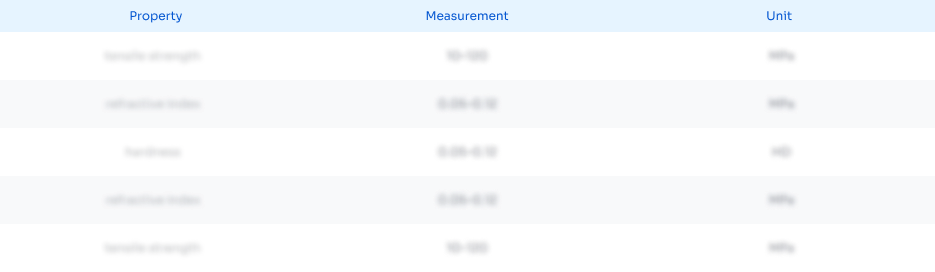
Abstract
Description
Claims
Application Information

- R&D
- Intellectual Property
- Life Sciences
- Materials
- Tech Scout
- Unparalleled Data Quality
- Higher Quality Content
- 60% Fewer Hallucinations
Browse by: Latest US Patents, China's latest patents, Technical Efficacy Thesaurus, Application Domain, Technology Topic, Popular Technical Reports.
© 2025 PatSnap. All rights reserved.Legal|Privacy policy|Modern Slavery Act Transparency Statement|Sitemap|About US| Contact US: help@patsnap.com