Densification method of porous workpiece
A densification and workpiece technology, which is used in the densification of porous parts, sintered porous parts and castings, and can solve the problem that the parts cannot have connected pores, cannot achieve hot isostatic pressing, and the glass is brittle. and other problems, to achieve the effect of high density and mechanical properties, improved packing density and low production cost
- Summary
- Abstract
- Description
- Claims
- Application Information
AI Technical Summary
Problems solved by technology
Method used
Image
Examples
example 1
[0035] The bevel gear made of SLS sintered Ni625 alloy powder to be dense and porous is as follows: figure 1 As shown, its diameter is 60 mm, and the initial relative density is 45%. The bevel gear has been degreased at high temperature before being densified by this method.
[0036] (1) Process a cylindrical sheath with an inner diameter of 70mm and a wall thickness of 2mm by machining. The material is 45 steel.
[0037] (2) Fix the bevel gear to the inner center of the sheath, and perform sealing welding on the connection between the sheath and the end cap.
[0038] (3) Check for leaks on the package. If there is air leakage in the sheath, it is necessary to re-seal the joint between the sheath and the end cap until there is no air leakage. If there is no air leak, go directly to the next step.
[0039] (4) Borosilicate glass powder is filled into the inside of the bag, and its composition is 78.5% SiO 2 , 14.6% B 2 o 3 , 4.9% Na 2 O, 1.8%Al 2 o 3 And a small amount...
example 2
[0047] The porous part to be densified is a cylinder formed by SLM of 316L stainless steel powder, with a diameter of 40 mm and an initial relative density of 78%.
[0048] (1) Process a cylindrical sheath with an inner diameter of 50mm and a wall thickness of 2mm by machining, and the material is 45 steel.
[0049] (2) Fix the 316L stainless steel SLM part to the inner center of the sheath, and seal the joint between the sheath and the end cap.
[0050] (3) Check for leaks on the package. If there is air leakage in the sheath, it is necessary to re-seal the joint between the sheath and the end cap until there is no air leakage. If there is no air leak, go directly to the next step.
[0051] (4) Soda-lime-silica glass powder is filled inside the sheath, the main component of which is 72.5% SiO 2 , 13.1%Na 2 O, 11.2% CaO, 1.8% Al 2 o 3 and a small amount of MgO, K 2 O, etc., the softening point temperature test is 729 ° C, shaking and shaking on a vibrating table.
[00...
example 3
[0059] The porous product to be densified is a cylinder formed by SLM of Ti-6Al-4V powder, with a diameter of 20 mm and an initial relative density of 68%.
[0060] (1) Process a cylindrical sheath with an outer diameter of 30mm and a wall thickness of 2mm by machining. The material is 45 steel.
[0061] (2) Fix the cylindrical SLM part to the inner center of the sheath, and perform sealing welding on the connection between the sheath and the end cap.
[0062] (3) Check for leaks on the package. If there is air leakage in the sheath, it is necessary to re-seal the joint between the sheath and the end cap until there is no air leakage. If there is no air leak, go directly to the next step.
[0063] (4) Borosilicate glass powder is filled into the inside of the bag, and its composition is 85% SiO 2 , 13.4% B 2 o 3 and a small amount of Na 2 O, Al 2 o 3 etc., the softening point temperature test is 820°C, and it is shaken and shaken on a vibrating table.
[0064] (5) Ins...
PUM
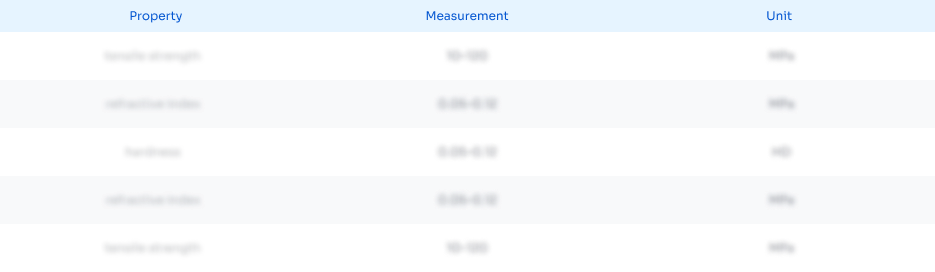
Abstract
Description
Claims
Application Information

- R&D Engineer
- R&D Manager
- IP Professional
- Industry Leading Data Capabilities
- Powerful AI technology
- Patent DNA Extraction
Browse by: Latest US Patents, China's latest patents, Technical Efficacy Thesaurus, Application Domain, Technology Topic, Popular Technical Reports.
© 2024 PatSnap. All rights reserved.Legal|Privacy policy|Modern Slavery Act Transparency Statement|Sitemap|About US| Contact US: help@patsnap.com