Fault-tolerant direct torque control method for six-phase permanent magnet synchronous motor lacking any two phases of windings
A technology of permanent magnet synchronous motor and direct torque control, which is applied in the fields of motor generator control, AC motor control, motor vibration suppression control, etc.
- Summary
- Abstract
- Description
- Claims
- Application Information
AI Technical Summary
Problems solved by technology
Method used
Image
Examples
Embodiment Construction
[0051] The present invention will be further described below in conjunction with the accompanying drawings and embodiments.
[0052] Please refer to figure 1 with Figure 4 , the present invention provides a six-phase permanent magnet synchronous motor lacking any two-phase fault-tolerant direct torque control method, which is characterized in that it includes the following steps:
[0053] The first step is to collect the remaining healthy phase C ~ F current i c ~i f and rotor position angle θ r ;
[0054] In the second step, using the T4 orthogonal transformation matrix in formula 1, the remaining healthy four-phase current i c ~i f Transformed to i in αβ coordinates sα i sβ and i in the zero-sequence axis system sz1 i sz2 :
[0055] T 4 = 0 - 1 2 ...
PUM
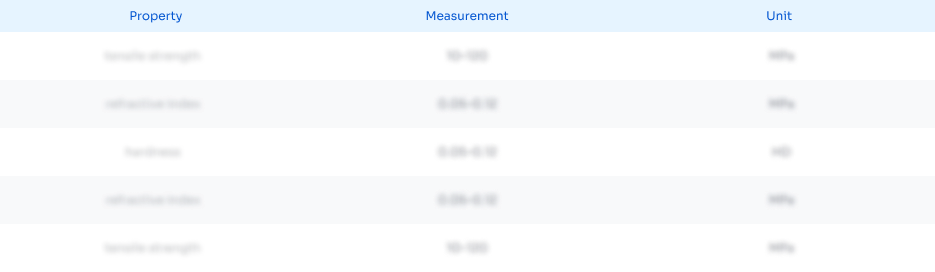
Abstract
Description
Claims
Application Information

- Generate Ideas
- Intellectual Property
- Life Sciences
- Materials
- Tech Scout
- Unparalleled Data Quality
- Higher Quality Content
- 60% Fewer Hallucinations
Browse by: Latest US Patents, China's latest patents, Technical Efficacy Thesaurus, Application Domain, Technology Topic, Popular Technical Reports.
© 2025 PatSnap. All rights reserved.Legal|Privacy policy|Modern Slavery Act Transparency Statement|Sitemap|About US| Contact US: help@patsnap.com