Wafer type ultrasonic non-destructive testing probe for low-modulus gear root residual stress
A technology of residual stress and non-destructive testing, which is applied to the analysis of solids using sound waves/ultrasonic waves/infrasonic waves, material analysis using sound waves/ultrasonic waves/infrasonic waves, and measuring devices. Service fatigue residual stress, low accuracy and other issues
- Summary
- Abstract
- Description
- Claims
- Application Information
AI Technical Summary
Problems solved by technology
Method used
Image
Examples
Embodiment Construction
[0013] The specific embodiment of the present invention is described in detail below:
[0014] 1. L CR wave excitation
[0015] According to Snell's law, when the ultrasonic longitudinal wave propagates from the slower acoustic wedge to the faster gear material, refraction will occur. When the longitudinal wave refraction angle is equal to 90°, the corresponding incident angle is called the first critical angle. Calculate The formula is shown below.
[0016] θ cr = sin -1 (V 1 / V 2 )
[0017] In the formula:
[0018] V 1 —propagation speed of ultrasonic longitudinal wave in medium with slow wave velocity (m / s);
[0019] V 2 — Propagation speed of ultrasonic longitudinal wave in medium with faster wave velocity (m / s).
[0020] θ cr - the first critical angle (°);
[0021] The critically refracted longitudinal wave will propagate along the surface near the tooth root of the gear.
[0022] According to the nature of the gear involute, find the tangent of the involut...
PUM
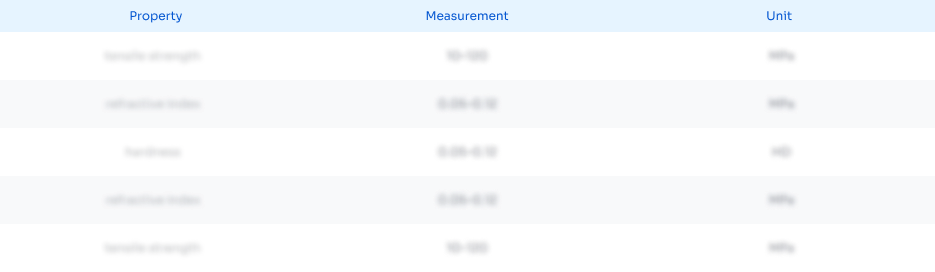
Abstract
Description
Claims
Application Information

- R&D
- Intellectual Property
- Life Sciences
- Materials
- Tech Scout
- Unparalleled Data Quality
- Higher Quality Content
- 60% Fewer Hallucinations
Browse by: Latest US Patents, China's latest patents, Technical Efficacy Thesaurus, Application Domain, Technology Topic, Popular Technical Reports.
© 2025 PatSnap. All rights reserved.Legal|Privacy policy|Modern Slavery Act Transparency Statement|Sitemap|About US| Contact US: help@patsnap.com