Preparation method of polyphenyl ether adhesive and copper-clad plate thereof
A polyphenylene ether and adhesive technology, applied in polyether adhesives, adhesives, adhesive additives, etc., can solve problems such as high melting temperature, limited application, and poor melt fluidity
- Summary
- Abstract
- Description
- Claims
- Application Information
AI Technical Summary
Problems solved by technology
Method used
Image
Examples
preparation example Construction
[0056] Preparation of modified low molecular weight polyphenylene ether resin:
[0057] Modified low molecular weight polyphenylene ether resin Ⅰ
[0058] First, add 100 kg of polyphenylene ether (Asahi Kasei Chemical Co., Ltd., trade name S201A, number average molecular weight is 20,000) in a non-airtight reactor A equipped with a reflux condenser, stirring, and a thermocouple, and add 240 kg of toluene As a solvent, raise the temperature to 90°C and stir to dissolve the polyphenylene ether particles completely, then add 15.5kg of diallyl bisphenol A, at 55°C, add 3.2kg of benzoyl peroxide, add in 6 times within 0.5h Complete, stop reaction after reacting 3h. Second, add 2.2kg of sodium hydroxide and 1kg of tetrabutylammonium bromide to reactor A, add 30kg of 3-chloropropene dropwise at a temperature of 50°C, drop it for 1 hour, and continue the reaction at this temperature After 8 hours, the reaction solution of allylated polyphenylene ether resin was obtained. Thirdly, d...
Embodiment 1
[0067] Take 100 kg of resin composition at room temperature (50 kg of the above-mentioned modified low molecular weight polyphenylene ether resin I, 29.4 kg of Dow 383 epoxy resin, 16 kg of bisphenol A benzoxazine resin, 4.6 kg of bismaleimide resin ㎏), 25 kg of magnesium hydroxide, 70 kg of toluene and 23 kg of methyl ethyl ketone were added to the plastic mixing tank, stirred for 1 hour, added 1.3 kg of imidazole, stirred at room temperature for 1 hour, and the molding time of the round hole method was 272 seconds under a hot plate at 171 °C. That is, the preparation of the polyphenylene ether adhesive is completed.
[0068] The glass fiber cloth 2116 is coated with polyphenylene ether adhesive through the gluing machine. The length of the drying channel of the gluing machine is 24m, divided into 3 sections, each section is 8m, and the baking temperature ranges from 70°C to 165°C. ℃, the speed (line speed) of the gluing machine is 2-10m / min, after the glass fiber cloth coate...
Embodiment 2
[0070]Take 100 kg of resin composition at room temperature (50 kg of the above-mentioned modified low molecular weight polyphenylene ether resin II, 26.8 kg of Dow 383 epoxy resin, 18 kg of bisphenol A benzoxazine resin, 5.2 kg of bismaleimide resin ㎏), talcum powder 26㎏, toluene 70㎏ and methyl ethyl ketone 23㎏ were added to the plastic mixing tank, stirred for 2 hours, added 1.3kg of triphenylphosphine, stirred at room temperature for 1 hour, and the molding time of the round hole method under a hot plate at 171°C was In 291 seconds, the preparation of the polyphenylene ether adhesive is completed.
[0071] The glass fiber cloth 2116 is coated with polyphenylene ether adhesive through the gluing machine. The length of the drying channel of the gluing machine is 24m, divided into 3 sections, each section is 8m, and the baking temperature ranges from 70°C to 165°C. ℃, the speed (line speed) of the gluing machine is 2-10m / min, after the glass fiber cloth coated with the polyphen...
PUM
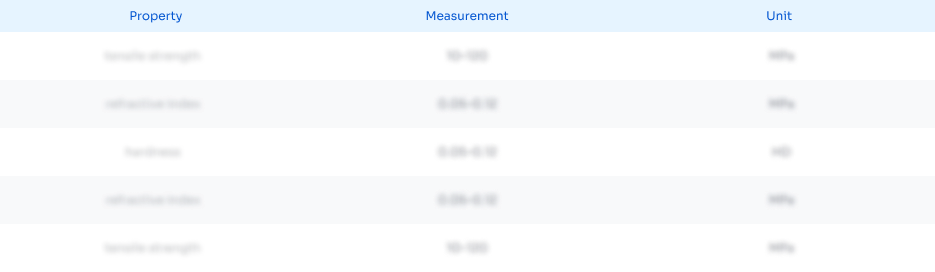
Abstract
Description
Claims
Application Information

- Generate Ideas
- Intellectual Property
- Life Sciences
- Materials
- Tech Scout
- Unparalleled Data Quality
- Higher Quality Content
- 60% Fewer Hallucinations
Browse by: Latest US Patents, China's latest patents, Technical Efficacy Thesaurus, Application Domain, Technology Topic, Popular Technical Reports.
© 2025 PatSnap. All rights reserved.Legal|Privacy policy|Modern Slavery Act Transparency Statement|Sitemap|About US| Contact US: help@patsnap.com