Preparation method of oil injection pump plunger surface phosphating liquid
A surface phosphating and preparation method technology, applied in the direction of metal material coating process, etc., can solve the problems of shortened product life, unusable, high phosphating temperature, etc., and achieve the effect of improving production efficiency, improving production efficiency, and low processing temperature
- Summary
- Abstract
- Description
- Claims
- Application Information
AI Technical Summary
Problems solved by technology
Method used
Examples
Embodiment 1
[0019] A method for preparing a phosphating solution on the plunger surface of a fuel injection pump. The phosphating solution is composed of: 85% phosphoric acid 10g / L, 68% nitric acid 8g / L, zinc oxide 16g / L, nickel nitrate 6g / L, iron nitrate 2g / L, copper nitrate 2g / L, sodium citrate 3g / L, tartaric acid 7g / L, sodium fluoroborate 1g / L, sodium chlorate 1.5g / L, hydrogen peroxide 1.5ml / L, sodium carbonate 4g / L, balance Be water; Described phosphating solution preparation method is:
[0020] (1) Take an appropriate amount of water to adjust the zinc oxide into a paste;
[0021] (2) Take an appropriate amount of water again, add phosphoric acid and nitric acid to prepare the mixed solution, then add the paste zinc oxide in step (1), and then put it into the reaction kettle;
[0022] (3) Add nickel nitrate, iron nitrate, copper nitrate, sodium citrate, tartaric acid, sodium fluoroborate, sodium chlorate, hydrogen peroxide, and sodium carbonate into the reaction kettle in sequence,...
Embodiment 2
[0024] A method for preparing a phosphating solution on the plunger surface of a fuel injection pump. The phosphating solution is composed of: 85% phosphoric acid 12g / L, 68% nitric acid 6g / L, zinc oxide 18g / L, nickel nitrate 4g / L, iron nitrate 4g / L, copper nitrate 1g / L, sodium citrate 5g / L, tartaric acid 5g / L, sodium fluoroborate 2g / L, sodium chlorate 0.5g / L, hydrogen peroxide 2.5ml / L, sodium carbonate 3g / L, balance Be water; Described phosphating solution preparation method is:
[0025] (1) Take an appropriate amount of water to adjust the zinc oxide into a paste;
[0026] (2) Take an appropriate amount of water again, add phosphoric acid and nitric acid to prepare the mixed solution, then add the paste zinc oxide in step (1), and then put it into the reaction kettle;
[0027] (3) Add nickel nitrate, iron nitrate, copper nitrate, sodium citrate, tartaric acid, sodium fluoroborate, sodium chlorate, hydrogen peroxide, and sodium carbonate into the reaction kettle in sequence,...
Embodiment 3
[0029] A method for preparing a phosphating solution on the plunger surface of a fuel injection pump. The phosphating solution is composed of: 85% phosphoric acid 11g / L, 68% nitric acid 7g / L, zinc oxide 17g / L, nickel nitrate 5g / L, iron nitrate 3g / L, copper nitrate 1.5g / L, sodium citrate 4g / L, tartaric acid 6g / L, sodium fluoroborate 1.5g / L, sodium chlorate 1g / L, hydrogen peroxide 2ml / L, sodium carbonate 3.5g / L, The amount is water; the preparation method of the phosphating solution is:
[0030] (1) Take an appropriate amount of water to adjust the zinc oxide into a paste;
[0031] (2) Take an appropriate amount of water again, add phosphoric acid and nitric acid to prepare the mixed solution, then add the paste zinc oxide in step (1), and then put it into the reaction kettle;
[0032] (3) Add nickel nitrate, iron nitrate, copper nitrate, sodium citrate, tartaric acid, sodium fluoroborate, sodium chlorate, hydrogen peroxide, and sodium carbonate into the reaction kettle in seq...
PUM
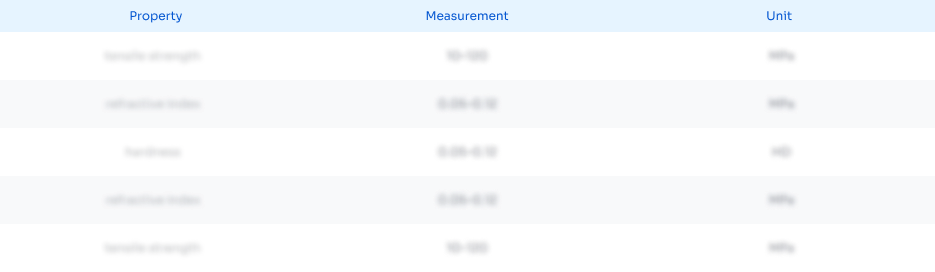
Abstract
Description
Claims
Application Information

- R&D Engineer
- R&D Manager
- IP Professional
- Industry Leading Data Capabilities
- Powerful AI technology
- Patent DNA Extraction
Browse by: Latest US Patents, China's latest patents, Technical Efficacy Thesaurus, Application Domain, Technology Topic, Popular Technical Reports.
© 2024 PatSnap. All rights reserved.Legal|Privacy policy|Modern Slavery Act Transparency Statement|Sitemap|About US| Contact US: help@patsnap.com