Manufacturing method of autoclaved fly ash-lime brick
An autoclaved fly ash brick and a manufacturing method technology, applied in the field of building material manufacturing, can solve the problems of many bad bricks, insufficient strength of finished bricks, and insufficient reaction, so as to achieve improved utilization efficiency, high finished product strength, and bad brick rate low effect
- Summary
- Abstract
- Description
- Claims
- Application Information
AI Technical Summary
Problems solved by technology
Method used
Image
Examples
Embodiment 1
[0021] The raw materials are: 63% of fly ash, 20% of stone chips, 15% of lime, and 2% of gypsum in percentage by weight. , the amount of water added is 15% of the total weight of fly ash, stone chips, lime and gypsum, and the temperature of the stirring slurry is controlled at 42°C; the mixture is then sent to the digestion bin for digestion, and the mixture passes through 6 The digestion of 1 hour is sent to the wheel mill by the disc feeder located under the digestion bin for adding water and rolling; the amount of water added to the wheel mill is 3% of the total weight of fly ash, stone chips, lime, and gypsum;
[0022] The rolled blank is sent into the hydraulic brick machine to be pressed into adobe, and then put into the autoclave for curing. The autoclaved curing section includes four stages of vacuum, boost, constant pressure and step-down. The constant pressure stage The pressure in the autoclave is 1.1 MPa and the temperature is 180° C., and the depressurization stag...
Embodiment 2
[0024] The raw materials are: 63% of fly ash, 20% of stone chips, 15% of lime, and 2% of gypsum in percentage by weight. , the amount of water added is 10% of the total weight of fly ash, stone chips, lime and gypsum, and the temperature of the stirring slurry is controlled at 38°C; the mixture is then sent to the digestion bin for digestion, and the mixture passes through 5 The digestion of 1 hour is sent to the wheel mill by the disc feeder located under the digestion bin for adding water and rolling; the amount of water added to the wheel mill is 2% of the total weight of fly ash, stone chips, lime, and gypsum;
[0025] The rolled blank is sent into the hydraulic brick machine to be pressed into adobe, and then put into the autoclave for curing. The autoclaved curing section includes four stages of vacuum, boost, constant pressure and step-down. The constant pressure stage The pressure in the autoclave is 0.9 MPa and the temperature is 170° C., and the depressurization stag...
Embodiment 3
[0027] The raw materials are: 63% of fly ash, 20% of stone chips, 15% of lime, and 2% of gypsum in percentage by weight. , the amount of water added is 13% of the total weight of fly ash, stone chips, lime and gypsum, and the temperature of the stirring slurry is controlled at 40°C; the mixture is then sent to the digestion bin for digestion, and the mixture passes through 5.5 The digestion of 1 hour is sent to the wheel mill by the disc feeder arranged under the digestion bin for adding water and rolling; the amount of water added to the wheel mill is 2.5% of the total weight of fly ash, stone chips, lime and gypsum;
[0028] The rolled blank is sent into the hydraulic brick machine to be pressed into adobe, and then put into the autoclave for curing. The autoclaved curing section includes four stages of vacuum, boost, constant pressure and step-down. The constant pressure stage The pressure in the autoclave is 1.0 MPa and the temperature is 175° C., and the depressurization ...
PUM
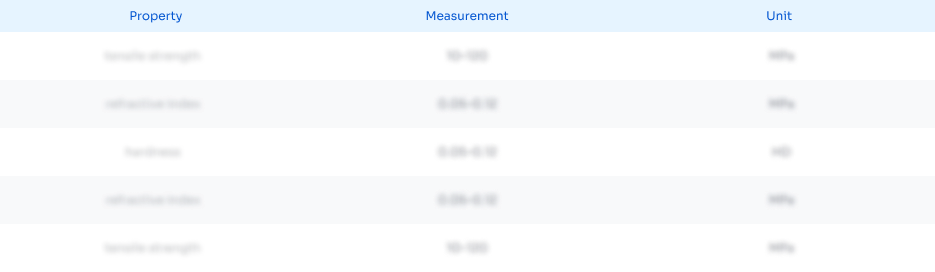
Abstract
Description
Claims
Application Information

- Generate Ideas
- Intellectual Property
- Life Sciences
- Materials
- Tech Scout
- Unparalleled Data Quality
- Higher Quality Content
- 60% Fewer Hallucinations
Browse by: Latest US Patents, China's latest patents, Technical Efficacy Thesaurus, Application Domain, Technology Topic, Popular Technical Reports.
© 2025 PatSnap. All rights reserved.Legal|Privacy policy|Modern Slavery Act Transparency Statement|Sitemap|About US| Contact US: help@patsnap.com