Slag fetching device used after slagging smelting and use method thereof
A kind of equipment and slag-making technology, which is applied in the field of slag-taking equipment after slagging and smelting, can solve the problems of polysilicon mixed with slag agent and difficult to separate, and achieve the effects of reducing energy consumption, effectively taking slag and dumping, saving production cycle and cost
- Summary
- Abstract
- Description
- Claims
- Application Information
AI Technical Summary
Problems solved by technology
Method used
Image
Examples
Embodiment 1
[0024] like figure 1 The shown slag extraction equipment after slag making and smelting includes a cantilever crane 1, a cantilever 2 is fixedly installed on the cantilever crane 1, a wire reel 3 is fixedly installed on the cantilever 2, and the wire reel 3 is suspended and connected with a slag storage device. 5. A closed cavity is formed between the inner wall and the outer wall of the slag storage device 5. The closed cavity is connected with a water inlet pipe 12 and a water outlet pipe 11. The slag storage device 5 is communicated with the vacuum tank 17 through the vacuum bellows 16. It is also communicated with the gas cylinder 21 through the blowing pipe 19, wherein the vacuum tank 17 is connected to the vacuum pump 13 through the connecting pipe 14, the bottom of the slag storage device 5 is communicated with a graphite tube 6, and a graphite crucible 7 is placed at the bottom of the outlet end of the graphite tube 6. An induction coil 8 is wound around the outer wall...
Embodiment 2
[0029] Use the equipment described in Example 1 to pick up the slag:
[0030] The first step of pretreatment: put the silicon material and slag material into the graphite crucible 7, start the power supply of the induction coil 8, and heat the silicon material and the slag material in the graphite crucible 7 to 1500 ° C to completely melt into a molten state to form silicon liquid 10 and slag agent 9, and keep warm at this temperature for 30min;
[0031] The second step is to inflate: control the winding machine 3 to make the slag storage device 5 descend until the bottom end of the graphite tube 6 descends to the bottom of the silicon liquid 10, open the gas valve 18 at this time, and pass the gas 20 into the molten silicon liquid 10, Make the gas 20 fully react with the molten silicon liquid 10;
[0032] The third step is slag extraction treatment: after the inflation process is completed, the gas valve 18 is closed, and the reel 3 is controlled to make the slag storage dev...
Embodiment 3
[0038] Use the equipment described in Example 1 to pick up the slag:
[0039] The first step of pretreatment: put the silicon material and slag material into the graphite crucible 7, start the power supply of the induction coil 8, and heat the silicon material and the slag material in the graphite crucible 7 to 1500 ° C to completely melt into a molten state to form silicon liquid 10 and slag agent 9, and keep warm at this temperature for 50min;
[0040] The second step is to inflate: control the winding machine 3 to make the slag storage device 5 descend until the bottom end of the graphite tube 6 descends to the bottom of the silicon liquid 10, open the gas valve 18 at this time, and pass the gas 20 into the molten silicon liquid 10, Make the gas 20 fully react with the molten silicon liquid 10;
[0041] The third step is slag extraction treatment: after the inflation process is completed, the gas valve 18 is closed, and the reel 3 is controlled to make the slag storage dev...
PUM
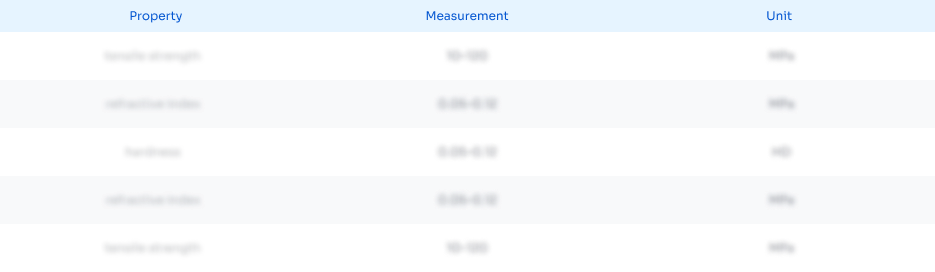
Abstract
Description
Claims
Application Information

- Generate Ideas
- Intellectual Property
- Life Sciences
- Materials
- Tech Scout
- Unparalleled Data Quality
- Higher Quality Content
- 60% Fewer Hallucinations
Browse by: Latest US Patents, China's latest patents, Technical Efficacy Thesaurus, Application Domain, Technology Topic, Popular Technical Reports.
© 2025 PatSnap. All rights reserved.Legal|Privacy policy|Modern Slavery Act Transparency Statement|Sitemap|About US| Contact US: help@patsnap.com