High-fluidity polylactic acid-based wood-plastic injection molding composite material and preparation method thereof
A composite material and high fluidity technology, applied in the field of degradable polylactic acid-based wood-plastic composite materials, can solve problems such as poor interface compatibility, achieve favorable processing and molding, reduce burning, and simple operation
- Summary
- Abstract
- Description
- Claims
- Application Information
AI Technical Summary
Problems solved by technology
Method used
Image
Examples
Embodiment 1
[0029] A preparation method of a graft copolymer of polylactic acid-glycidyl methacrylate: add 20 g of dried polylactic acid into a flask containing 100 mL of DMF, feed nitrogen, and add 2 g of glycidyl methacrylate and 0.1 g DCP initiator. The reaction was placed in a microwave reactor with a microwave power of 400W, and the reaction was stirred for 10 minutes. Precipitate with ethanol, filter and dry to obtain the compatibilizer.
[0030] Mix poplar wood fiber (80-mesh poplar wood powder, the same below), polylactic acid, polycaprolactone, lubricant and compatibilizer according to the mass ratio of 50 / 50 / 10 / 1 / 10, add the twin-screw In the silo of the extruder, the temperature of the screw is set to 170° C., and the rotational speed of the screw is 150 rpm. The extrudate is cooled and pelletized to obtain composite material particles.
Embodiment 2
[0032] The preparation method of the graft copolymer of polylactic acid-glycidyl methacrylate: add 20 g of dried polylactic acid into a flask containing 120 mL of DMF, blow nitrogen into the system, and add 4 g of glycidyl methacrylate and 0.15 g of DCP Initiator. The reaction was placed in a microwave reactor with a microwave power of 600W, and the reaction was stirred for 15 minutes. Precipitate with ethanol, filter and dry to obtain the compatibilizer.
[0033] Poplar wood fiber, polylactic acid, polycaprolactone, lubricant and compatibilizer are mixed according to the ratio of 50 / 50 / 10 / 1 / 5 by mass, and added to the silo of the twin-screw extruder, and the screw temperature is set to 195°C, screw speed 280rpm. The extrudate is cooled and pelletized to obtain composite material particles.
Embodiment 3
[0035]A preparation method of a graft copolymer of polylactic acid-glycidyl methacrylate: a preparation method of a graft copolymer of polylactic acid-glycidyl methacrylate: add 20 g of dried polylactic acid into a flask containing 80 mL of DMF , nitrogen gas was passed into the system, and 1.5 g of glycidyl methacrylate and 0.15 g of BPO initiator were added to the system. The reaction was placed in a microwave reactor with a microwave power of 400W, and the reaction was stirred for 12 minutes. Precipitate with ethanol, filter and dry to obtain the compatibilizer.
[0036] Poplar wood fiber, polylactic acid, polycaprolactone, lubricant and compatibilizer are mixed according to the ratio of 50 / 45 / 5 / 2 / 13 by mass, and added to the silo of the twin-screw extruder, and the screw temperature is set to 180°C, screw speed 260rpm. The extrudate is cooled and pelletized to obtain composite material particles.
PUM
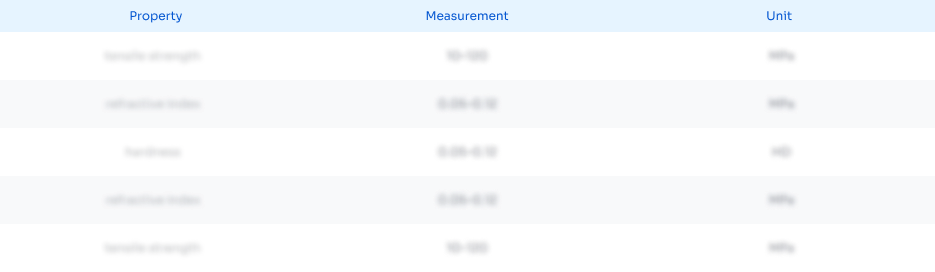
Abstract
Description
Claims
Application Information

- R&D
- Intellectual Property
- Life Sciences
- Materials
- Tech Scout
- Unparalleled Data Quality
- Higher Quality Content
- 60% Fewer Hallucinations
Browse by: Latest US Patents, China's latest patents, Technical Efficacy Thesaurus, Application Domain, Technology Topic, Popular Technical Reports.
© 2025 PatSnap. All rights reserved.Legal|Privacy policy|Modern Slavery Act Transparency Statement|Sitemap|About US| Contact US: help@patsnap.com