Impurity removing process for enhancing quality of silicon carbide fine micro powder
A silicon carbide, fine and micro technology, which is applied in the field of impurity removal process to improve the quality of silicon carbide fine powder, can solve the problem of high content of free carbon and ferric oxide, the content of fine particles and fine powder is easy to exceed the standard, and the quality of silicon carbide fine powder is not good. Stability and other issues, to achieve high quality and cleanliness, improve cleanliness, and improve the effect
- Summary
- Abstract
- Description
- Claims
- Application Information
AI Technical Summary
Problems solved by technology
Method used
Examples
Embodiment 1
[0027] Put the silicon carbide fine powder into the mixing tank, add deionized water to prepare a slurry with a mass concentration of 30%, and after stirring evenly, send the slurry to the turnover cylinder, which is connected to the flotation column through pipelines, and turns to the turnover Add the quaternary ammonium salt blowing agent (such as dodecyl dimethyl benzyl ammonium chloride) and the polyoxyethylene of 0.01% of the total weight of the slurry in the slurry in the cylinder, and then put The slurry is sent to the flotation column for flotation carbon removal, air is introduced from the bottom of the flotation column, and the foam generated on the slurry surface is removed, and the slurry flowing out of the outlet of the flotation column is sent to the wet magnetic separator through the pipeline Carry out magnetic separation to remove iron, and send the slurry treated by the wet magnetic separator to the turnover tank again, add water to adjust its concentration to ...
Embodiment 2
[0029] Put the silicon carbide fine powder into the mixing tank, add deionized water to prepare a slurry with a mass concentration of 50%, and after stirring evenly, send the slurry to the turnover cylinder, which is connected to the flotation column through a pipeline to the turnover Add 0.01% sulfonyl hydrazide foaming agent and 0.01% polyoxyethylene to the slurry in the cylinder, then send the slurry to the flotation column for flotation decarbonization, from the flotation Air is introduced into the bottom of the column to remove the foam generated on the slurry surface. The slurry flowing out of the outlet of the flotation column is sent to the wet magnetic separator through the pipeline for magnetic separation and iron removal. The slurry treated by the wet magnetic separator Send it to the turnover tank again, add water to adjust its concentration to 50%, and add foaming agent of 0.01% of the total weight of the slurry after adjusting the concentration and polyoxyethylene...
Embodiment 3
[0031]Put the silicon carbide fine powder into the mixing tank, add deionized water to prepare a slurry with a mass concentration of 40%, and after stirring evenly, send the slurry to the turnover cylinder, which is connected to the flotation column through pipelines, and turns to the turnover Add the sodium dodecylbenzenesulfonate of 0.01% of the total weight of slurry and the polyoxyethylene of 0.01% of the total weight of slurry in the slurry in the cylinder, then send the slurry to the flotation column for flotation decarbonization, from Air is introduced into the bottom of the flotation column to remove the foam generated on the slurry surface. The slurry flowing out of the outlet of the flotation column is sent to the wet magnetic separator through the pipeline for magnetic separation and iron removal. The material treated by the wet magnetic separator The slurry is sent to the turnover tank again, and the concentration is adjusted to 40% by adding water, and the foaming ...
PUM
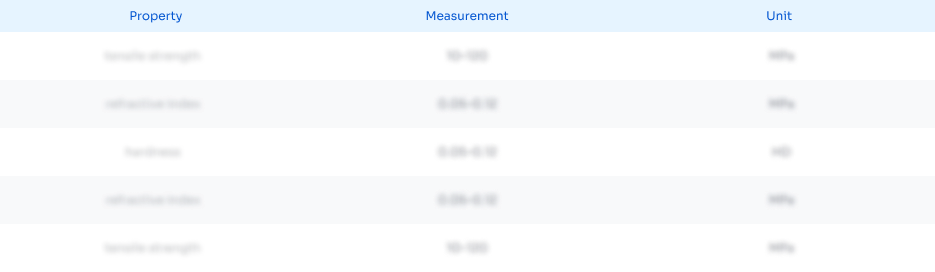
Abstract
Description
Claims
Application Information

- R&D
- Intellectual Property
- Life Sciences
- Materials
- Tech Scout
- Unparalleled Data Quality
- Higher Quality Content
- 60% Fewer Hallucinations
Browse by: Latest US Patents, China's latest patents, Technical Efficacy Thesaurus, Application Domain, Technology Topic, Popular Technical Reports.
© 2025 PatSnap. All rights reserved.Legal|Privacy policy|Modern Slavery Act Transparency Statement|Sitemap|About US| Contact US: help@patsnap.com