Asynchronous motor direct torque control method based on synthesized voltage vectors
A technology of direct torque control and asynchronous motor, which is applied in motor generator control, electronic commutation motor control, vector control system, etc., and can solve the problem of poor torque performance, excessive torque fluctuation, flux linkage trajectory distortion, etc. problem, achieve the effect of reducing fluctuation and flux linkage trajectory distortion, reducing torque fluctuation and improving torque performance
- Summary
- Abstract
- Description
- Claims
- Application Information
AI Technical Summary
Problems solved by technology
Method used
Image
Examples
Embodiment Construction
[0033] The present invention will be further described in detail below in conjunction with the examples, which are not intended to limit the present invention.
[0034] like figure 1 As shown, the asynchronous motor direct torque control system based on the synthetic voltage vector technology provided by this embodiment includes a synthetic voltage vector PWM output signal controller 1, an estimation module 2, a torque hysteresis controller 3, and a flux linkage PI controller 4, voltage vector selection table 5, PI speed controller 6, inverter 7, stator voltage and current collector 8, asynchronous motor 9, speed observer 10. This system is a double closed-loop control system, in which the inner loop controls the torque and flux linkage of the asynchronous motor, and the outer loop uses a PI speed controller 6, which is compared with the motor speed collected by the speed observer 10 and the given value After that, a given torque value T is generated e * , to control the mo...
PUM
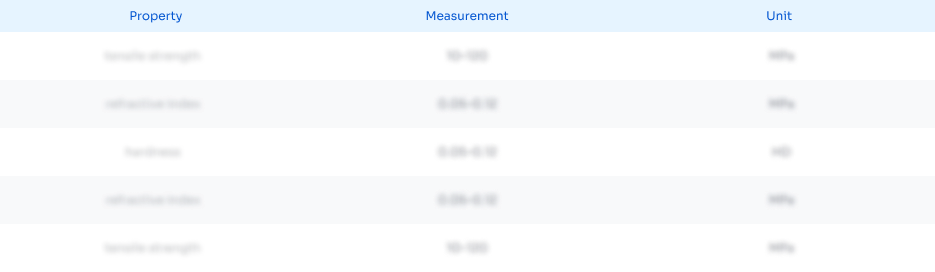
Abstract
Description
Claims
Application Information

- R&D Engineer
- R&D Manager
- IP Professional
- Industry Leading Data Capabilities
- Powerful AI technology
- Patent DNA Extraction
Browse by: Latest US Patents, China's latest patents, Technical Efficacy Thesaurus, Application Domain, Technology Topic, Popular Technical Reports.
© 2024 PatSnap. All rights reserved.Legal|Privacy policy|Modern Slavery Act Transparency Statement|Sitemap|About US| Contact US: help@patsnap.com