A kind of carbon fiber surface modification method
A surface modification, carbon fiber technology, applied in the direction of carbon fiber, fiber treatment, textile and papermaking, etc., can solve the problems of carbon fiber performance degradation, carbon fiber erosion and other problems, to achieve the effect of improving the interface performance and improving the resistance to atomic oxygen
- Summary
- Abstract
- Description
- Claims
- Application Information
AI Technical Summary
Problems solved by technology
Method used
Image
Examples
specific Embodiment approach 1
[0031] Specific embodiment 1: This embodiment provides a method for modifying the surface of carbon fibers, which is specifically completed according to the following steps:
[0032] 1. Cleaning
[0033] Put 6g of carbon fibers into a Soxhlet extractor filled with acetone, extract with acetone at a temperature of 60°C, and remove the sizing agent and impurities on the surface of the carbon fibers. The cleaning time is 12 hours. Dry in a blast drying oven to obtain cleaned carbon fibers.
[0034] 2. Oxidation
[0035] (1) Put 2 g of dry and cleaned carbon fibers obtained in step 1 into a 250 ml round bottom flask, add 100 ml of concentrated nitric acid, and oxidize at 60 ° C for 2 h. The concentrated nitric acid concentration is 68%.
[0036] (2) Soak 2g of oxidized carbon fibers obtained in step 2 (1) in 100ml of distilled water for 5 minutes, take out the carbon fibers soaked in distilled water, and discard the distilled water.
[0037] (3) Repeat step 2 (2) 5 times to ob...
specific Embodiment approach 2
[0043] Specific embodiment two: This embodiment provides a carbon fiber surface modification method, which is specifically completed according to the following steps:
[0044] 1. Cleaning
[0045] Put 6g of carbon fiber into a Soxhlet extractor filled with acetone, extract with acetone at a temperature of 70°C, and remove the sizing agent and impurities on the surface of the carbon fiber. The cleaning time is 32 hours. Dry in a blast drying oven to obtain cleaned carbon fibers.
[0046] 2. Oxidation
[0047] (1) Put 2g of dry and cleaned carbon fibers obtained in step 1 into a 250ml round bottom flask, add 100ml of concentrated nitric acid, and oxidize at 80°C for 3h. The concentrated nitric acid concentration is 68%.
[0048] (2) Soak 2g of the oxidized carbon fiber obtained in step 2 (1) in 100ml of distilled water for 10 minutes, take out the carbon fiber soaked in distilled water, and discard the distilled water.
[0049](3) Repeat step 2 (2) 5 times to obtain the clea...
specific Embodiment approach 3
[0055] Specific embodiment three: This embodiment provides a method for modifying the surface of carbon fibers, which is specifically completed according to the following steps:
[0056] 1. Cleaning
[0057] Put 6g of carbon fiber into a Soxhlet extractor filled with acetone, and use acetone to extract at a temperature of 80°C to remove the sizing agent and impurities on the surface of the carbon fiber. The cleaning time is 48 hours. Dry in a blast drying oven to obtain cleaned carbon fibers.
[0058] 2. Oxidation
[0059] (1) Put 2g of dry and cleaned carbon fibers obtained in step 1 into a 250ml round bottom flask, add 30ml of concentrated nitric acid and 90ml of concentrated sulfuric acid, and oxidize at 80°C for 3h. The described concentrated nitric acid concentration is 68%, and the concentrated sulfuric acid concentration is 68%.
[0060] (2) Soak 2g of the oxidized carbon fiber obtained in step 2 (1) in 100ml of distilled water for 10 minutes, take out the carbon fib...
PUM
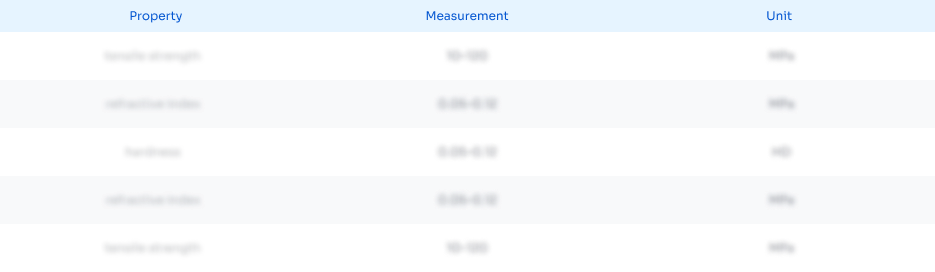
Abstract
Description
Claims
Application Information

- R&D
- Intellectual Property
- Life Sciences
- Materials
- Tech Scout
- Unparalleled Data Quality
- Higher Quality Content
- 60% Fewer Hallucinations
Browse by: Latest US Patents, China's latest patents, Technical Efficacy Thesaurus, Application Domain, Technology Topic, Popular Technical Reports.
© 2025 PatSnap. All rights reserved.Legal|Privacy policy|Modern Slavery Act Transparency Statement|Sitemap|About US| Contact US: help@patsnap.com