Cemented quenching heat treatment method of automobile engine gears
A heat treatment method and technology for automobile engines, which are applied in heat treatment furnaces, heat treatment equipment, furnace types, etc., can solve problems such as grinding failure of more than 15-20%, reduce gear qualification rate, affect production efficiency, etc., to improve the use of life, improve the qualified rate of finished products and production efficiency, and improve the effect of comprehensive mechanical properties
- Summary
- Abstract
- Description
- Claims
- Application Information
AI Technical Summary
Problems solved by technology
Method used
Image
Examples
Embodiment 1
[0025] Embodiment 1: the carburizing and quenching heat treatment method of the automobile engine gear of the present invention, the method comprises: carrying out carburizing and quenching treatment to the gear after forging, pre-selection heat treatment, turning and gear hobbing, and the carburizing and quenching treatment Including the following steps:
[0026] a) A plurality of gears are stacked on a tooling washer 1 with an intermediate round rod 3, and an upper cover plate 2 is arranged on it to form a group of gear strings;
[0027] b) Send multiple sets of gear strings into Aichelin5 / 3 multi-purpose furnace for carburizing and quenching. In the step b: first heat the gear strings to 850 ° C for 0.5 hours, with a carbon potential of 0.4%, and then heat to 930 ° C for infiltration Carbon, strong carburizing potential 1.15%, strong infiltration time 140 minutes, then transfer to diffusion, diffusion carbon potential 0.75%, time 110 minutes, then cool down with the furnace...
Embodiment 2
[0030] Embodiment 2: the carburizing and quenching heat treatment method of the automobile engine gear of the present invention, the method comprises: carrying out carburizing and quenching treatment to the gear after forging, pre-selection heat treatment, turning and gear hobbing, and described carburizing and quenching treatment Including the following steps:
[0031] a) A plurality of gears are stacked on a tooling washer 1 with an intermediate round rod 3, and an upper cover plate 2 is arranged on it to form a group of gear strings;
[0032] b) Send multiple groups of gear strings into Aichelin5 / 3 multi-purpose furnace for carburizing and quenching. The specific process of carburizing and quenching is: first heat the gear strings to 800 ° C for 0.2 hours, carbon potential 0.3%, and then heat to 920 ° C Carburizing, strong carburizing potential 1.2%, strong infiltration time 160 minutes, then transfer to diffusion, diffusion carbon potential 0.73%, time 130 minutes, then co...
Embodiment 3
[0035] Embodiment 3: the carburizing and quenching heat treatment method of the automobile engine gear of the present invention, the method comprises: carrying out carburizing and quenching treatment to the gear after forging, pre-selection heat treatment, turning and gear hobbing, and the carburizing and quenching treatment Including the following steps:
[0036] a) A plurality of gears are stacked on a tooling washer 1 with an intermediate round rod 3, and an upper cover plate 2 is arranged on it to form a group of gear strings;
[0037] b) Send multiple groups of gear strings into Aichelin5 / 3 multi-purpose furnace for carburizing and quenching. The specific carburizing and quenching process is: first heat the gear strings to 860°C for 0.8 hours, carbon potential 0.5%, and then heat to 910°C Carburizing, strong carburizing potential 1.2%, strong infiltration time 170 minutes, then transfer to diffusion, diffusion carbon potential 0.78%, time 120 minutes, then cool down with ...
PUM
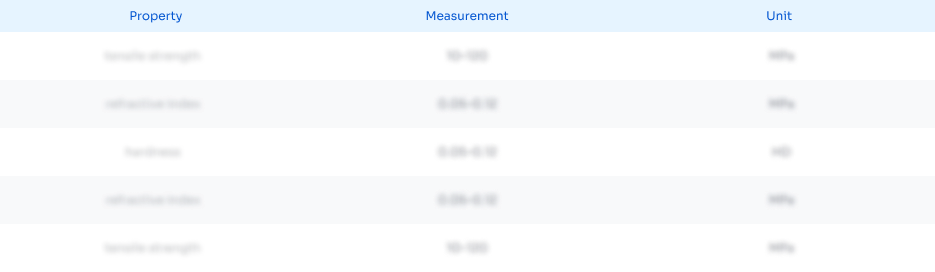
Abstract
Description
Claims
Application Information

- Generate Ideas
- Intellectual Property
- Life Sciences
- Materials
- Tech Scout
- Unparalleled Data Quality
- Higher Quality Content
- 60% Fewer Hallucinations
Browse by: Latest US Patents, China's latest patents, Technical Efficacy Thesaurus, Application Domain, Technology Topic, Popular Technical Reports.
© 2025 PatSnap. All rights reserved.Legal|Privacy policy|Modern Slavery Act Transparency Statement|Sitemap|About US| Contact US: help@patsnap.com