Power generation system using heating furnace waste heat integrally
A power generation system and heating furnace technology, which is applied to lighting and heating equipment, furnaces, waste heat treatment, etc., can solve problems such as waste of energy, achieve the effects of improving thermal efficiency, prolonging service life, and improving thermal efficiency of power generation
- Summary
- Abstract
- Description
- Claims
- Application Information
AI Technical Summary
Problems solved by technology
Method used
Image
Examples
Embodiment 1
[0016] Such as figure 1 As shown, the waste heat recovered in this embodiment includes two parts: the waste heat of the cooling water beam in the furnace of the heating furnace and the flue gas at about 350° C. in the tail flue of the heating furnace. A steam-water cooling heat exchanger 16 is arranged in the hearth of the heating furnace 1 to absorb the waste heat of the cooling water beam. In the tail flue, a high-pressure superheated steam heat exchanger 2, a low-pressure superheated steam heat exchanger 3, and a low-pressure evaporation tube bundle heat exchanger 4 are arranged in sequence according to the flue gas flow direction, to absorb the waste heat of the flue gas. The end of the tail flue is connected with the induced draft fan 6, and the induced draft fan 6 is connected with the chimney 7. After the high-temperature flue gas generated by combustion in the furnace of the heating furnace preheats the air and gas, the temperature of the flue gas is reduced to about ...
Embodiment 2
[0029] Such as figure 2 As shown, in this embodiment, on the basis of the above-mentioned embodiment 1, an economizer 5 is arranged in the tail flue, and the economizer is arranged after the low-pressure evaporation tube bundle heat exchanger according to the flow direction of the flue gas. The condenser 10 of the condensing steam turbine 8 is connected to the inlet of the economizer through a condensate pump 11, and the outlet of the economizer is connected to the low-pressure steam drum, and the condensate recovered by the condenser is in the After absorbing heat in the economizer, it enters the low-pressure steam drum 12.
[0030] In this case, the exhaust steam at the tail of the steam-enhancing condensing steam turbine 8 passes through the condenser 10 and becomes condensed water, which is pumped into the economizer 5 by the condensed water pump 11 to absorb the low-temperature waste heat of the flue gas, and the water after absorbing heat enters the In the low-pressure...
Embodiment 3
[0034] The difference between this embodiment and the above-mentioned embodiment 1 is that: the high pressure in the high-pressure saturated steam and the high-pressure superheated steam in this embodiment is 0.8Mpa, and the low pressure in the low-pressure saturated steam and the low-pressure superheated steam is 0.2MPa.
PUM
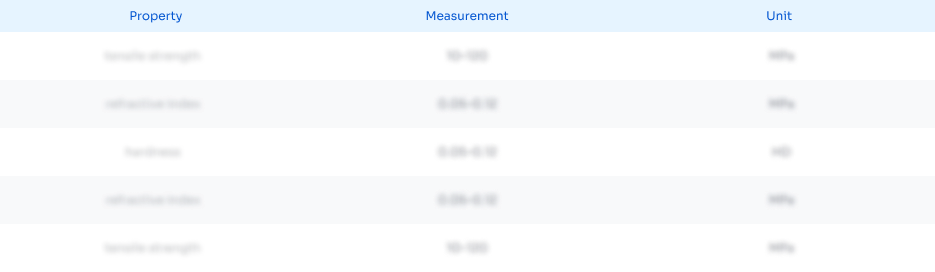
Abstract
Description
Claims
Application Information

- R&D
- Intellectual Property
- Life Sciences
- Materials
- Tech Scout
- Unparalleled Data Quality
- Higher Quality Content
- 60% Fewer Hallucinations
Browse by: Latest US Patents, China's latest patents, Technical Efficacy Thesaurus, Application Domain, Technology Topic, Popular Technical Reports.
© 2025 PatSnap. All rights reserved.Legal|Privacy policy|Modern Slavery Act Transparency Statement|Sitemap|About US| Contact US: help@patsnap.com