Rectangular concrete filled steel tube column and steel beam single-side bolt connecting joint and construction method thereof
A technology of unilateral bolts and rectangular steel pipes, which is applied in the direction of construction and building construction, can solve the problems of buckling damage, bearing capacity, stiffness, ductility and poor energy dissipation capacity, achieve high energy consumption capacity, realize standardized production, Good plasticity and ductility
- Summary
- Abstract
- Description
- Claims
- Application Information
AI Technical Summary
Problems solved by technology
Method used
Image
Examples
Embodiment 1
[0037] The structure of this embodiment is as follows figure 1 , figure 2 As shown, the outer reinforcing plate 6 is composed of two channel steels, and each channel steel is made by tailor-welding three steel plates or cold-formed by a steel plate. First, the steel beam 4 and the end plate 3 are welded firmly, and then the two The block channel steel and the pipe wall of the steel pipe column 1 are reliably connected by surrounding welding, and then bolt holes are opened at the corresponding positions of the wall of the steel pipe column 1, the channel steel web and the end plate 3 for the installation of unilateral bolts 5. During on-site construction, the steel The beam 4 is hoisted to the designated position, the unilateral bolt 5 is tightened with a torque wrench, and the end plate 3, the outer reinforcing plate 6 and the wall of the steel pipe column 1 are connected reliably. Finally, concrete 2 is poured in the steel pipe column 1 to complete the construction of the jo...
Embodiment 2
[0039] The structure of this embodiment is as follows image 3 , Figure 4 As shown, first make the built-in short H-beam 7, the width and height of its section are slightly smaller than the width and height of the inner side wall of the section of the steel pipe column 1, and its length is slightly larger than the height of the section of the steel beam 3, and then the short H-beam 7 is inserted into the node core and spot welding with the inner wall of the steel pipe column 1, then the steel beam 4 and the end plate 3 are welded firmly, and bolt holes are opened at the corresponding positions of the steel pipe column 1 wall, the built-in short H-beam 7 and the end plate 3 for the installation of unilateral Bolt 5. During on-site construction, hoist the steel beam 3 to the designated position, tighten the unilateral bolt 4 with a torque wrench, and connect the end plate 3, the flange of the built-in short H-beam 7 and the wall of the steel pipe column 1 reliably. Concrete 2 ...
Embodiment 3
[0041] The structure of this embodiment is as follows Figure 5 , Image 6 As shown, firstly, the plug welding hole is opened on the wall of the steel pipe column 1, and the restraint rod 8 is reliably connected with the pipe walls on both sides through the plug welding seam at the opening, and then the steel beam 4 and the end plate 3 are welded firmly, and then the steel pipe column 1 is welded firmly. Bolt holes are opened at the corresponding positions of the wall and end plate 3 for installing unilateral bolts 5. During on-site construction, hoist the steel beam 4 to the designated position, tighten the unilateral bolts 5 with a torque wrench, and connect the end plate 3 to the steel pipe column 1. The walls are connected reliably, and finally concrete 2 is poured in the steel pipe column 1 to complete the construction of the joint.
PUM
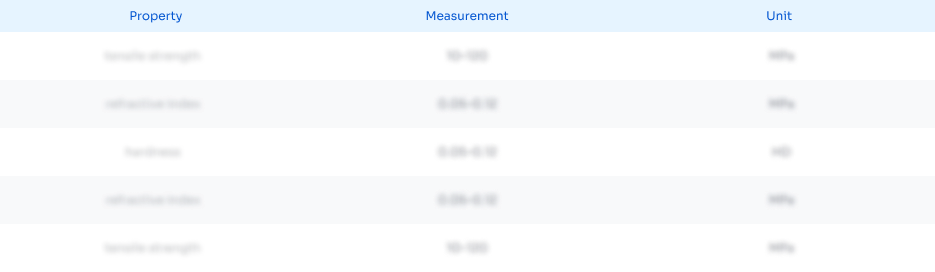
Abstract
Description
Claims
Application Information

- R&D Engineer
- R&D Manager
- IP Professional
- Industry Leading Data Capabilities
- Powerful AI technology
- Patent DNA Extraction
Browse by: Latest US Patents, China's latest patents, Technical Efficacy Thesaurus, Application Domain, Technology Topic, Popular Technical Reports.
© 2024 PatSnap. All rights reserved.Legal|Privacy policy|Modern Slavery Act Transparency Statement|Sitemap|About US| Contact US: help@patsnap.com