Piston ring manufacturing process beneficial to chromium plating quality
A manufacturing process, piston ring technology, applied in the field of piston ring manufacturing process, can solve the problems of increased air leakage of piston rings, poor processing technology, increased fuel consumption, etc., to reduce machining allowance and improve service life , the effect of slowing down the amount of wear
- Summary
- Abstract
- Description
- Claims
- Application Information
AI Technical Summary
Problems solved by technology
Method used
Examples
Embodiment 1
[0017] Piston ring manufacturing process conducive to chrome plating quality, including clamping, inner and outer circle profiling, insert groove forming, chamfering of outer corners, chrome plating, outer circle forming grinding and honing steps;
[0018] The mosaic groove forming step adopts cutting treatment;
[0019] The turning process includes two processes of rough turning and finish turning, and the finish turning process includes two working steps of semi-finish turning and finish turning.
[0020] Compared with the existing technology, the process route determined above is that the clamping step is set before the mosaic groove forming and chrome plating steps, and the mosaic groove forming is processed by turning, so that in this process route, the inner and outer circles are profiling and inlaid at one time. Groove cutting and chrome plating can be completed on the same rotary shaft, and the piston needs to be clamped to the forming mill, and the cutting tools used ...
Embodiment 2
[0022] This embodiment is further limited on the basis of Embodiment 1: a further technical solution is: in order to further ensure the quality of the product, the honing step further includes an inspection step.
[0023] In order to eliminate the phenomenon of uneven chrome plating, improve the service life of the product and the accuracy of matching with the cylinder body, the cylindrical forming grinder includes the contour grinding process of the left and right grooves of the inlay groove after the chrome plating of the inlay groove.
PUM
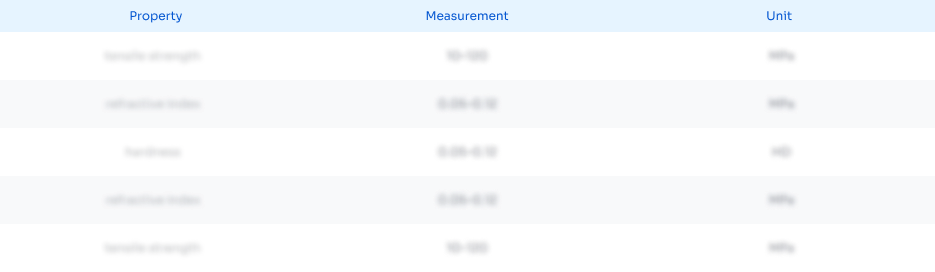
Abstract
Description
Claims
Application Information

- R&D Engineer
- R&D Manager
- IP Professional
- Industry Leading Data Capabilities
- Powerful AI technology
- Patent DNA Extraction
Browse by: Latest US Patents, China's latest patents, Technical Efficacy Thesaurus, Application Domain, Technology Topic, Popular Technical Reports.
© 2024 PatSnap. All rights reserved.Legal|Privacy policy|Modern Slavery Act Transparency Statement|Sitemap|About US| Contact US: help@patsnap.com