Vibrating diaphragm forming mold base and vibrating diaphragm forming mold including the mold base
A technology of forming molds and forming seats, which is applied in the direction of sensors and electrical components, can solve the problems of easy wrinkling of the diaphragm, improper forming of the diaphragm, and poor stability, and achieve excellent acoustic performance, clear outline, and high stability.
- Summary
- Abstract
- Description
- Claims
- Application Information
AI Technical Summary
Problems solved by technology
Method used
Image
Examples
Embodiment 1
[0030] Such as figure 1 As shown, a diaphragm forming mold seat includes a diaphragm forming seat 20a consistent with the structure of the diaphragm to be processed, and a base 10 is arranged around the diaphragm forming seat 20a, and the diaphragm forming seat 20a and the base 10 is integrated, and the diaphragm molding seat 20a includes a straight side part 22a, a corner part 26a and a spherical top part 24a that are combined together.
[0031] Such as figure 2 and image 3 Commonly shown, the straight edge portion 22a, the corner portion 26a and the dome top 24a are processed from two kinds of materials such as aluminum, copper, stainless steel and air-permeable steel, wherein the materials of the straight edge portion 22a and the corner portion 26a are different, straight The side 22a is made of the same material as the dome top 24a. In this embodiment, it is preferable that both the straight edge portion 22a and the spherical top portion 24a are made of aluminum, and ...
Embodiment 2
[0035] This embodiment is basically the same as Embodiment 1, the difference is that:
[0036] Such as Figure 4 , Figure 5 and Figure 6 As shown collectively, the diaphragm molding seat 20b includes a straight edge portion 22b, a corner portion 26b and a spherical top portion 24b. The straight edge portion 22b, the spherical top portion 24b and the corner portion 26b are separately processed from three materials among aluminum, copper, stainless steel and air-permeable steel. In this embodiment, preferably, the straight edge portion 22b is processed from aluminum, the ball top 24b is processed from copper, and the corner portion 26b is processed from air-permeable steel.
[0037] Such as Figure 6 As shown, the straight edge portion 22b is made of the same material as the base 10, which is aluminum.
[0038] Such as Figure 4 , Figure 5 and Figure 6 As shown together, the base 10 and the straight side part 22b have an integrated structure, which is formed by one-t...
PUM
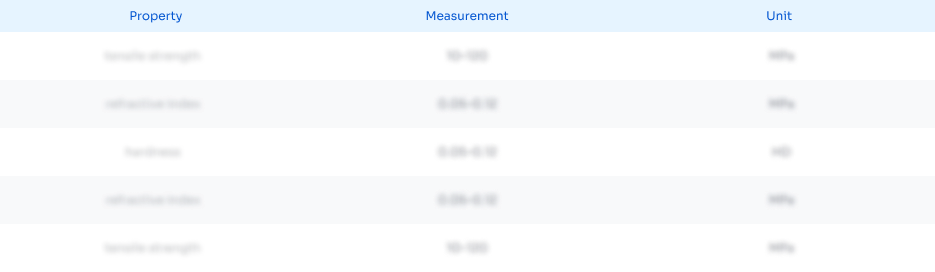
Abstract
Description
Claims
Application Information

- R&D Engineer
- R&D Manager
- IP Professional
- Industry Leading Data Capabilities
- Powerful AI technology
- Patent DNA Extraction
Browse by: Latest US Patents, China's latest patents, Technical Efficacy Thesaurus, Application Domain, Technology Topic, Popular Technical Reports.
© 2024 PatSnap. All rights reserved.Legal|Privacy policy|Modern Slavery Act Transparency Statement|Sitemap|About US| Contact US: help@patsnap.com