Method for recovering waste heat of high-temperature fuel gas of smelting furnace
A high-temperature flue gas and smelting furnace technology, which is applied in the field of industrial furnaces and flue gas waste heat resource recovery and utilization, can solve the problems of inconvenient component control, inability to fully recover high-temperature flue gas, and small capacity of smelting furnaces, so as to improve the efficiency of waste heat recovery , improve the life of dust removal equipment, and ensure the effect of safe and stable operation
- Summary
- Abstract
- Description
- Claims
- Application Information
AI Technical Summary
Problems solved by technology
Method used
Image
Examples
Embodiment Construction
[0022] The specific embodiment of the present invention is further described below in conjunction with accompanying drawing:
[0023] Such as figure 1 As shown, the high-temperature flue gas waste heat recovery system of the smelting furnace includes a smelting furnace 1, a regenerative burner system, a smoke exhaust fan 6, a flue gas circulation fan 7, and a convective radiation heat exchanger 12; where the furnace end of the smelting furnace 1 is set Choke fire wall 4, settling chamber 5 behind the choking fire wall, the flue exhaust channel of settling chamber 5 communicates with chimney 8 through convection radiation heat exchanger 12, regenerative burner system is set on both sides of smelting furnace 1, heat storage The regenerative burner system includes a regenerative burner 2, a regenerator 13 and a three-way reversing valve connected to the regenerative burner. A smoke return channel is set on the flue connecting the convective radiation heat exchanger 12 and the ch...
PUM
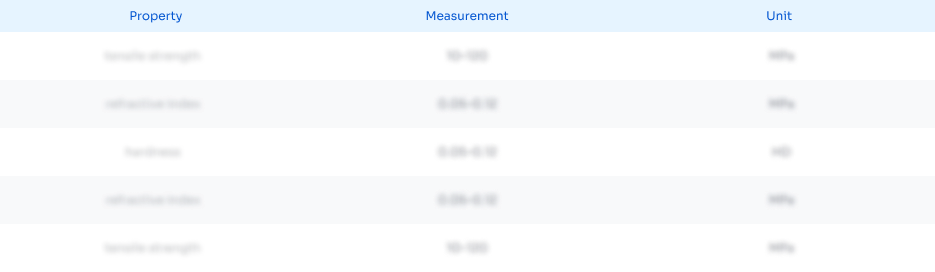
Abstract
Description
Claims
Application Information

- R&D Engineer
- R&D Manager
- IP Professional
- Industry Leading Data Capabilities
- Powerful AI technology
- Patent DNA Extraction
Browse by: Latest US Patents, China's latest patents, Technical Efficacy Thesaurus, Application Domain, Technology Topic, Popular Technical Reports.
© 2024 PatSnap. All rights reserved.Legal|Privacy policy|Modern Slavery Act Transparency Statement|Sitemap|About US| Contact US: help@patsnap.com