Method for preparation of high performance carbon fiber protofilament by blending method
A carbon fiber precursor, high-performance technology, applied in the direction of spinning solution preparation, fiber chemical characteristics, and complete sets of equipment for the production of artificial threads, can solve the problems of poor spinnability, high tensile strength, and small denier of polyacrylonitrile. Achieve the effect of reducing Ballas effect and high fiber strength
- Summary
- Abstract
- Description
- Claims
- Application Information
AI Technical Summary
Problems solved by technology
Method used
Examples
Embodiment 1
[0018] According to the formula in Table 1, mix high isotacticity and high molecular weight polyacrylonitrile evenly, then add dimethyl sulfoxide, dissolve the polymer in a step-by-step heating method, stir and swell at room temperature at low speed for 2 hours, and then raise the temperature to 40°C at a medium speed Stir and dissolve for 2 hours, then stir and dissolve at a high and uniform speed at 80°C for 48 hours to obtain a polyacrylonitrile spinning solution, and the temperature of the spinning solution is 60°C. The spinning solution is defoamed and filtered at 60°C, and after being metered by a metering pump, it is extruded from the spinneret holes of the spinneret and enters the first coagulation bath with a temperature of 40°C and a DMSO concentration of 80wt%. Then, it is coagulated and formed through a secondary coagulation bath with a temperature of 45°C and a DMSO concentration of 50wt% and a third-stage coagulation bath with a temperature of 50°C and a DMSO conc...
Embodiment 2
[0022] According to the formula in Table 2, mix high isotacticity and high molecular weight polyacrylonitrile evenly, then add dimethyl sulfoxide, dissolve the polymer by heating up in stages, stir and swell at room temperature at low speed for 2 hours, and then raise the temperature to 40°C at a medium speed Stir and dissolve for 2 hours, then stir and dissolve at a high and uniform speed at 80°C for 48 hours to obtain a polyacrylonitrile spinning solution, and the temperature of the spinning solution is 60°C. The spinning solution is defoamed and filtered at 60°C, and after being metered by a metering pump, it is extruded from the spinneret holes of the spinneret and enters the first coagulation bath with a temperature of 40°C and a DMSO concentration of 80wt%. Then, it is coagulated and formed through a secondary coagulation bath with a temperature of 45°C and a DMSO concentration of 50wt% and a third-stage coagulation bath with a temperature of 50°C and a DMSO concentration...
Embodiment 3
[0026] According to the formula in Table 3, mix high isotacticity and high molecular weight polyacrylonitrile evenly, then add dimethyl sulfoxide, dissolve the polymer in a step-by-step heating method, stir and swell at room temperature at low speed for 2 hours, and then raise the temperature to 40°C at a medium speed Stir and dissolve for 2 hours, then stir and dissolve at a high and uniform speed at 80°C for 48 hours to obtain a polyacrylonitrile spinning solution, and the temperature of the spinning solution is 60°C. The spinning solution is defoamed and filtered at 60°C, and after being metered by a metering pump, it is extruded from the spinneret holes of the spinneret and enters the first coagulation bath with a temperature of 40°C and a DMSO concentration of 80wt%. Then, it is coagulated and formed through a secondary coagulation bath with a temperature of 45°C and a DMSO concentration of 50wt% and a third-stage coagulation bath with a temperature of 50°C and a DMSO conc...
PUM
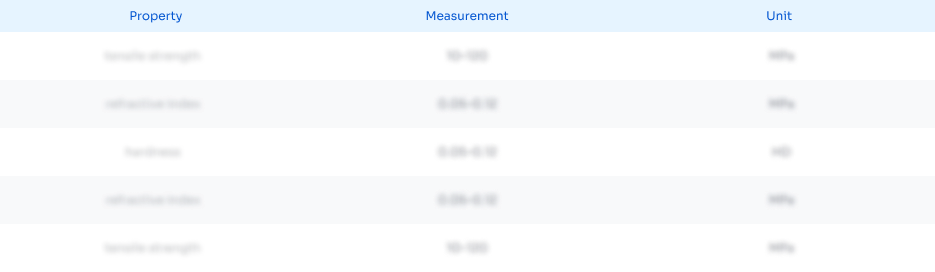
Abstract
Description
Claims
Application Information

- R&D
- Intellectual Property
- Life Sciences
- Materials
- Tech Scout
- Unparalleled Data Quality
- Higher Quality Content
- 60% Fewer Hallucinations
Browse by: Latest US Patents, China's latest patents, Technical Efficacy Thesaurus, Application Domain, Technology Topic, Popular Technical Reports.
© 2025 PatSnap. All rights reserved.Legal|Privacy policy|Modern Slavery Act Transparency Statement|Sitemap|About US| Contact US: help@patsnap.com