Piezoelectric principle-based omnidirectional horizontal shear guided wave transducer
A horizontal shearing, transducer technology, applied in instruments, scientific instruments, ultrasonic/sonic/infrasonic waves, etc., can solve the problem of generating the same guided waves, and achieve the effect of small volume
- Summary
- Abstract
- Description
- Claims
- Application Information
AI Technical Summary
Problems solved by technology
Method used
Image
Examples
Embodiment 1
[0019] An omnidirectional horizontal shear guided wave transducer based on the piezoelectric principle, including a plurality of piezoelectric sensitive elements 1 (dimensions such as 2mm×2mm×0.5mm, or 3mm×3mm×0.5mm, with a total outer diameter of 28mm) and temporary adhesive tape base 2, a plurality of piezoelectric sensitive elements are arranged in a circle to form an axisymmetric sensor array, the lower surface of the sensor array is pasted on the temporary adhesive tape base in advance to fix the shape of the sensor array, and the number of piezoelectric sensitive elements is 8 or 16, to ensure that the generated waveforms are continuous and uniform around the transducer. Each individual piezoelectric sensitive element has two electrodes, and the positive and negative electrodes 3.4 are located on the same surface. Wires are used to connect the positive electrodes of all piezoelectric sensitive elements. The electrodes are connected in series, and then all the negative ele...
Embodiment 2
[0021] The piezoelectric sensitive element used in the present invention is cut in the relaxation ferroelectric single crystal material, such as (1-x)Pb(Mg 1 / 3 Nb 2 / 3 )O 3 -PbTiO 3 (PMNT, lead magnesium niobate-lead titanate) and Pb(In 0.5 Nb 0.5 )O 3 -Pb(Mg 1 / 3 Nb 2 / 3 )O 3 -PbTiO 3 (PIN-PMN-PT, lead indium niobate-lead magnesium niobate-lead titanate), the specific polarization and cutting direction are as follows figure 2 (a) shown. [001], [010], [100] and [011] in the figure are the Miller indices representing the crystal orientation in crystallography, (011) represents the Miller index of the crystal plane, and the [011] direction and the (011) plane perpendicular to each other. x, y, z represent the coordinate system where the original crystal is placed, and the z direction is the growth direction of the crystal. First, the crystal is polarized along the [011] direction, that is, the Z direction, and then cut out a plane (011) perpendicular to this direction,...
Embodiment 3
[0023] The invention can be directly pasted on the surface of the measured structure and used for excitation of horizontal shear guided waves. Figure 4 An embodiment of the transducer for a thin aluminum plate is given. First, paste it completely on the surface of the cleaned aluminum plate with 502 and other super glue. After the glue is completely cured and the transducer is firmly bonded to the surface of the aluminum plate, a signal generator can be used to apply a voltage signal with a specified amplitude and center frequency (such as V pp = 40 volts, a five-peak narrow-band waveform with a center frequency of 120 kHz), thereby exciting a horizontal shear guided wave in the aluminum plate. Figure 5 to Figure 8 The experimental results of horizontal shear guided wave excitation in an aluminum plate are given, where the excitation voltage is V pp = 5 volts, center frequencies are 80kHz and 120kHz respectively. in Figure 5 with Image 6 is the test result in the dire...
PUM
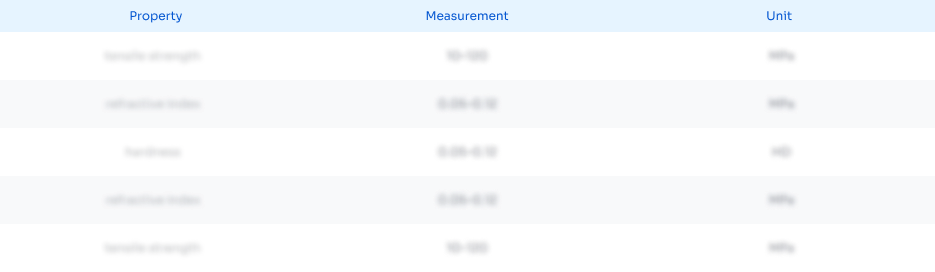
Abstract
Description
Claims
Application Information

- R&D
- Intellectual Property
- Life Sciences
- Materials
- Tech Scout
- Unparalleled Data Quality
- Higher Quality Content
- 60% Fewer Hallucinations
Browse by: Latest US Patents, China's latest patents, Technical Efficacy Thesaurus, Application Domain, Technology Topic, Popular Technical Reports.
© 2025 PatSnap. All rights reserved.Legal|Privacy policy|Modern Slavery Act Transparency Statement|Sitemap|About US| Contact US: help@patsnap.com