Spinning wheel intensive-cooling die
A strong cooling, wheel technology, applied in manufacturing tools, casting molding equipment, casting molds, etc., can solve the problems of low material utilization, large investment, slow heat dissipation, etc., and achieve extended mold life, large thermal conductivity, and elastic modulus. small effect
- Summary
- Abstract
- Description
- Claims
- Application Information
AI Technical Summary
Problems solved by technology
Method used
Image
Examples
Embodiment 1
[0013] Embodiment 1: The inner diameter of the copper tubes in the copper tube group is 4 mm, the wall thickness is 0.5 mm, the distance between the copper tubes is 2 mm, and the distance between the copper tubes and the molding wall is 3 mm.
Embodiment 2
[0014] Embodiment 2: The inner diameter of the copper tubes in the copper tube group is 6 mm, the wall thickness is 1.5 mm, the distance between the copper tubes is 4 mm, and the distance between the copper tubes and the molding wall is 10 mm.
Embodiment 3
[0015] Embodiment 3: The inner diameter of the copper tubes in the copper tube group is 8 mm, the wall thickness is 2 mm, the distance between the copper tubes is 8 mm, and the distance between the copper tubes and the molding wall is 20 mm.
PUM
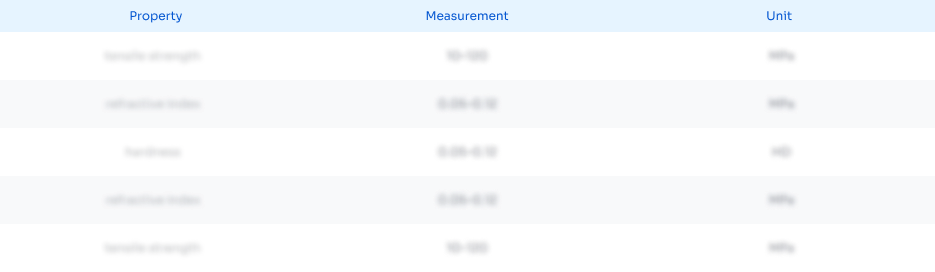
Abstract
Description
Claims
Application Information

- R&D
- Intellectual Property
- Life Sciences
- Materials
- Tech Scout
- Unparalleled Data Quality
- Higher Quality Content
- 60% Fewer Hallucinations
Browse by: Latest US Patents, China's latest patents, Technical Efficacy Thesaurus, Application Domain, Technology Topic, Popular Technical Reports.
© 2025 PatSnap. All rights reserved.Legal|Privacy policy|Modern Slavery Act Transparency Statement|Sitemap|About US| Contact US: help@patsnap.com