Stibnite flotation technology
An antimony and flotation technology, applied in flotation, solid separation and other directions, can solve the problems of reducing the lead content of antimony concentrate, weak collection capacity, low antimony recovery rate, etc. Work environment and effect of reducing antimony smelting cost
- Summary
- Abstract
- Description
- Claims
- Application Information
AI Technical Summary
Problems solved by technology
Method used
Image
Examples
Embodiment 1
[0022] Take 1000g of antimony stibnite ore containing 3.6wt% antimony, grind it to 77% and pass through a 0.074mm sieve hole at a concentration of 66.7wt%, add water to make the pulp concentration 35wt%, add 1.5g sulfuric acid and 0.1g lead nitrate and stir evenly , the PH value of the ore pulp measured by the PH test paper is 5.5, add 0.25g of medicament MA-1 and 0.1g of butyl xanthate mixed collector, and then add 0.11g of No. 2 oil and stir evenly before flotation. After the "two-sweep" flotation, the antimony concentrate with a grade of 47.06%, a recovery rate of 97.0% and a lead content of 0.091% was obtained, and the grade of antimony in the tailings was 0.18%.
Embodiment 2
[0024] Take 1000g of antimony stibnite ore containing 3.6wt% antimony, and grind it to 77% to pass through a 0.074mm sieve hole at a concentration of 70wt%, add water to make the slurry concentration 40wt%, add 1.5g sulfuric acid and 0.1g lead nitrate and stir evenly, The PH value of the pulp measured by the PH test paper is 5, add 0.1g of the agent MA-1 and 0.1g of butyl xanthate as a mixed collector, and then add 0.11g of No. 2 oil and stir evenly before flotation. After "sweeping" flotation, the antimony concentrate with a grade of 47.06%, a recovery rate of 96.70% and a lead content of 0.090% was obtained, and the grade of antimony in the tailings was 0.17%.
Embodiment 3
[0026] Put 78.36t of antimony-containing 2.2wt% antimony stibnite through 2130 ball mill, in the case of grinding concentration 74wt%, 1.5m diameter classifier overflow concentration 32wt%, overflow particle size -0.074mm is 72%, in a mixing tank Add 39.18kg of sulfuric acid and 7.54kg of lead nitrate to stir, and the pH test paper shows that the pH value is 6.0. Add 11.75kg and 7.84kg of MA-1 and butyl xanthate respectively in the secondary mixing tank, and add 8.62kg of No. 2 oil. After the flotation of "coarse, two cleaning and two fine", the antimony concentrate with a grade of 45.8%, a recovery rate of 93.6% and a lead content of 0.099% was obtained, and the grade of antimony in the tailings was 0.21%.
PUM
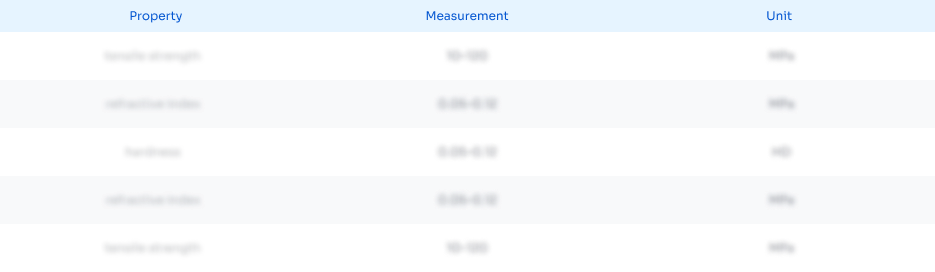
Abstract
Description
Claims
Application Information

- Generate Ideas
- Intellectual Property
- Life Sciences
- Materials
- Tech Scout
- Unparalleled Data Quality
- Higher Quality Content
- 60% Fewer Hallucinations
Browse by: Latest US Patents, China's latest patents, Technical Efficacy Thesaurus, Application Domain, Technology Topic, Popular Technical Reports.
© 2025 PatSnap. All rights reserved.Legal|Privacy policy|Modern Slavery Act Transparency Statement|Sitemap|About US| Contact US: help@patsnap.com