Cyanide-free monovalent copper presoaking method of steel and iron parts and zinc alloy die castings
A zinc alloy and die-casting technology, which is applied in metal material coating technology, liquid chemical plating, coating, etc., can solve the problems of poor bonding force of copper plating, and achieve the purpose of improving the bonding force of the plating layer, reducing the concentration, and reducing the discharge potential Effect
- Summary
- Abstract
- Description
- Claims
- Application Information
AI Technical Summary
Problems solved by technology
Method used
Image
Examples
specific Embodiment approach 1
[0014] Specific embodiment one: the iron and steel parts of the present embodiment and the zinc alloy die-casting part cyanide-free monovalent copper pre-impregnated copper method are carried out according to the following steps:
[0015] (1) Preparation of cyanide-free monovalent copper immersion plating solution: a. The concentration of monovalent copper compound is 2~40g / L, the concentration of antioxidant is 2~30g / L, and the concentration of non-cyanide main complexing agent is 10~130g / L, the concentration of auxiliary complexing agent is 5~60g / L, and the concentration of buffering agent is 5~40g / L. Weigh the monovalent copper compound, antioxidant, non-cyanide main complexing agent, auxiliary complexing agent b. the antioxidants taken by step a are dissolved in the hydrochloric acid solution of 60mL / L, then the non-cyanide main complexing agent and auxiliary complexing agent taken by step a are added, and under the condition of heating Stir until dissolved to prepare solu...
specific Embodiment approach 2
[0019] Specific embodiment two: the difference between this embodiment and specific embodiment one is that the monovalent copper compound described in a and c of step (1) is one of cuprous oxide, cuprous chloride or cuprous bromide , the concentration is 3~35g / L. Others are the same as in the first embodiment.
specific Embodiment approach 3
[0020] Specific embodiment three: the difference between this embodiment and specific embodiment one or two is that the stabilizer described in a and b of step (1) is hydroquinone, pyrocatechol, resorcinol, sub- One or a combination of sodium phosphate, uric acid or ascorbic acid, the concentration is 3~25g / L. Others are the same as in the first or second embodiment.
[0021] When the stabilizer of this embodiment is a composition, various stabilizers are combined in arbitrary ratios.
PUM
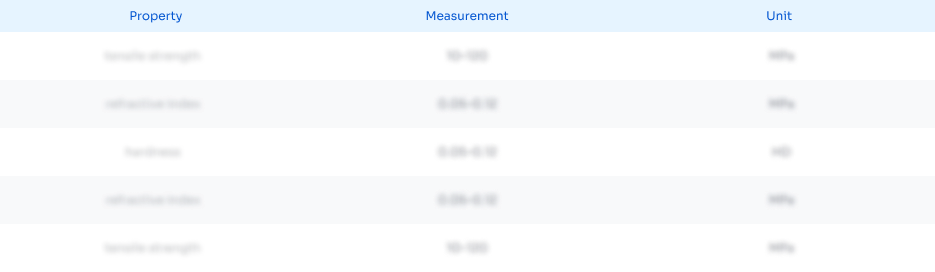
Abstract
Description
Claims
Application Information

- R&D Engineer
- R&D Manager
- IP Professional
- Industry Leading Data Capabilities
- Powerful AI technology
- Patent DNA Extraction
Browse by: Latest US Patents, China's latest patents, Technical Efficacy Thesaurus, Application Domain, Technology Topic, Popular Technical Reports.
© 2024 PatSnap. All rights reserved.Legal|Privacy policy|Modern Slavery Act Transparency Statement|Sitemap|About US| Contact US: help@patsnap.com