Fringe effect based capacitance type micro inertial sensor with self-calibrating
An inertial sensor, edge effect technology, applied in the direction of electric solid devices, instruments, circuits, etc., can solve the problems of inability to meet batch calibration, expensive vibration table, low calibration efficiency, etc., achieve novel structure, reduce Brown noise, reduce Effects of mechanical noise and circuit noise
- Summary
- Abstract
- Description
- Claims
- Application Information
AI Technical Summary
Problems solved by technology
Method used
Image
Examples
Embodiment Construction
[0017] Such as figure 1 , 2 , 3 and 4, a micro-inertial sensor with self-calibration includes a glass substrate 1, a sensor mass 22, and a fixed detection silicon strip 14.
[0018] The sensor mass 22 is provided with two groups of gate-shaped silicon strips 23 for sensitive detection in the X direction (there is a gap 20 between the silicon strips) and two groups of gate-shaped silicon strips for sensitive detection in the Y direction 19. The silicon strip group 23 for sensitive detection in the X direction and the silicon strip group 19 for sensitive detection in the Y direction are arranged in a staggered pattern, that is, a pair of silicon strip groups 23 for sensitive detection in the X direction are diagonally opposite, and a pair of silicon strip groups 23 for sensitive detection in the Y direction are arranged diagonally. The silicon strip group 19 for sensitive detection in the Y direction is also at an oblique angle. Two groups of grid-shaped silicon strip groups 23...
PUM
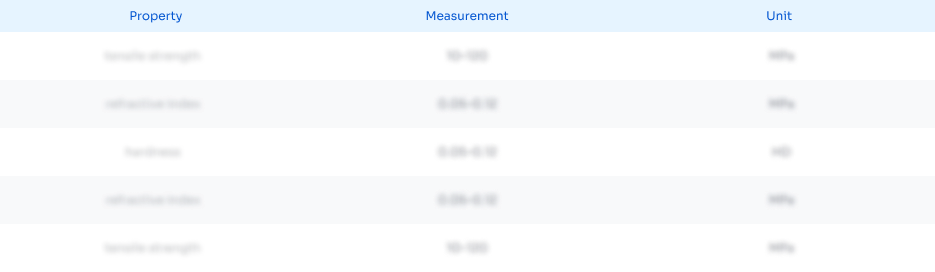
Abstract
Description
Claims
Application Information

- R&D Engineer
- R&D Manager
- IP Professional
- Industry Leading Data Capabilities
- Powerful AI technology
- Patent DNA Extraction
Browse by: Latest US Patents, China's latest patents, Technical Efficacy Thesaurus, Application Domain, Technology Topic, Popular Technical Reports.
© 2024 PatSnap. All rights reserved.Legal|Privacy policy|Modern Slavery Act Transparency Statement|Sitemap|About US| Contact US: help@patsnap.com