High-pressure dissolution-out and evaporation combined energy-saving method in production of aluminium oxide
A high-pressure dissolution, medium-high pressure technology, applied in the direction of alumina/hydroxide, etc., can solve the problems of low utilization efficiency, waste of heat, high comprehensive energy consumption of alumina, etc., to reduce production energy consumption and cost, good economic benefits and Social benefits, the effect of improving technical and economic indicators
- Summary
- Abstract
- Description
- Claims
- Application Information
AI Technical Summary
Problems solved by technology
Method used
Image
Examples
Embodiment 1
[0013] The domestic diaspore-type bauxite is processed by the high-temperature Bayer method, with a high-pressure dissolution temperature of 260°C and 280°C new steam heating. The new steam condensate generated by the new steam is flashed to 0.6MPa at the first stage, and the flash steam is sent to the mother liquor evaporation process through pipelines to partially replace the evaporated new steam. Save 16.3kg standard coal per ton of alumina.
Embodiment 2
[0015] The domestic diaspore-type bauxite is processed by the high-temperature Bayer method, with a high-pressure dissolution temperature of 280°C and 300°C new steam heating. The new steam condensate generated by the new steam is flashed to 0.4MPa in two stages, and the flash steam is sent to the mother liquor evaporation process through pipelines to partially replace the evaporated new steam. The 0.4MPa flash steam generated from the 6th stage pulp flash evaporation is sent to the mother liquor evaporation process through the pipeline to replace the new steam. Save 20.7kg standard coal per ton of alumina.
Embodiment 3
[0017] The domestic diaspore-type bauxite is treated by the high-temperature Bayer method, the high-pressure dissolution temperature is 280°C, and the molten salt is heated at 320°C. The 1MPa flash steam generated from the fifth-stage pulp flash evaporation is sent to the mother liquor evaporation process through the pipeline to replace the new steam for evaporation. Save 15.9kg standard coal per ton of alumina.
PUM
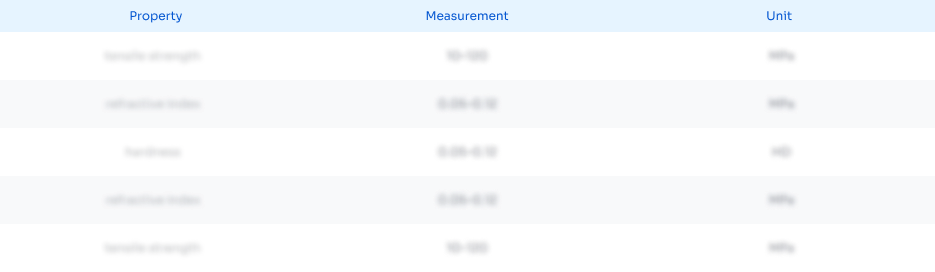
Abstract
Description
Claims
Application Information

- R&D
- Intellectual Property
- Life Sciences
- Materials
- Tech Scout
- Unparalleled Data Quality
- Higher Quality Content
- 60% Fewer Hallucinations
Browse by: Latest US Patents, China's latest patents, Technical Efficacy Thesaurus, Application Domain, Technology Topic, Popular Technical Reports.
© 2025 PatSnap. All rights reserved.Legal|Privacy policy|Modern Slavery Act Transparency Statement|Sitemap|About US| Contact US: help@patsnap.com