Condensate water desalination heat exchange mixed exhaust steam recovery secondary deoxygenation exhaust steam condensing device
A technology of exhaust steam recovery and secondary deoxygenation, applied in chemical instruments and methods, liquid degassing, separation methods, etc., can solve problems such as aggravating waste heat emissions, affecting safe operation of equipment, wasting waste heat resources and water resources, etc. To achieve the effect of exacerbating the emission of waste heat
- Summary
- Abstract
- Description
- Claims
- Application Information
AI Technical Summary
Problems solved by technology
Method used
Image
Examples
Embodiment Construction
[0032] Such as figure 1As shown, the condensed water desalination water heat exchange mixed exhaust steam recovery secondary deoxygenation exhaust steam condensing device includes a closed pressure buffer tank E1, a third heat exchanger H3 and a fourth heat exchanger H4. 135°C~ Calciner condensate at 155°C enters calciner condensate pipe S1, fluidized bed condensate at 135°C~155°C enters fluidized bed condensate pipe S2, dry ammonium condensate at 135°C~155°C enters dry ammonium condensate pipe, 60 ℃~80℃ synthetic ammonia cooling demineralized water enters synthetic ammonia demineralized water pipe Y1, 60℃~95 ℃ transform cooling demineralized water enters transformation demineralized water pipe Y2, calciner condensate pipe S1, fluidized bed condensate pipe S2 and dry ammonium condensate pipe S3 is respectively connected to the condensate water collection pipe S0, and other condensate water pipes S4 can also be connected to the condensate water collection pipe S0.
[0033] The...
PUM
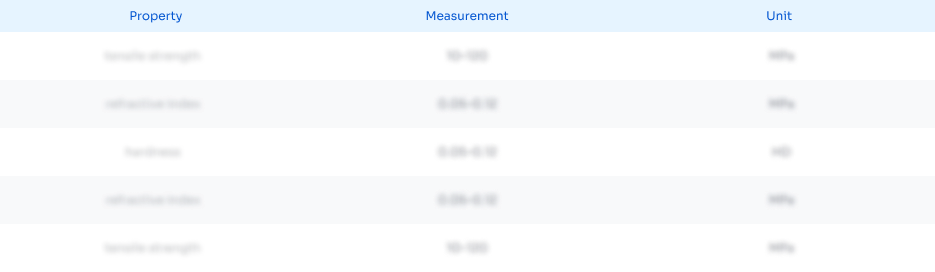
Abstract
Description
Claims
Application Information

- R&D
- Intellectual Property
- Life Sciences
- Materials
- Tech Scout
- Unparalleled Data Quality
- Higher Quality Content
- 60% Fewer Hallucinations
Browse by: Latest US Patents, China's latest patents, Technical Efficacy Thesaurus, Application Domain, Technology Topic, Popular Technical Reports.
© 2025 PatSnap. All rights reserved.Legal|Privacy policy|Modern Slavery Act Transparency Statement|Sitemap|About US| Contact US: help@patsnap.com