Energy-saving cooling toughening filling master batch and preparation method thereof
A filling masterbatch and toughening technology, which is applied in the field of energy-saving, cooling and toughening filler masterbatch and its preparation, can solve the problems of affecting the tensile strength of plastic woven bags, reducing the tensile strength of woven bags, and destroying the molecular structure of plastics. To achieve the effects of increasing tension, reducing consumption and cost, and improving quality
- Summary
- Abstract
- Description
- Claims
- Application Information
AI Technical Summary
Problems solved by technology
Method used
Examples
Embodiment 1
[0016] An energy-saving, cooling and toughening filler masterbatch, the weight percentage of each component is: 60% of ground calcium carbonate, 10% of dispersant, 20% of carrier resin, 5% of cooling agent, 1% of antioxidant, toughening Agent 2%, coupling agent 2%.
[0017] Preparation method: First, accurately weigh each component according to weight, put the weighed items (except the cooling agent) in a high-speed mixer for high-speed mixing, and release the material until it is completely coated. After the material is completely cooled, put it into the high-speed mixer again for low-speed mixing, add the measured cooling agent, and discharge the material after it is completely mixed evenly. The mixed materials are put into a twin-screw extruder for extrusion, granulation, packaging, and finished products.
Embodiment 2
[0019] An energy-saving, cooling and toughening filler masterbatch, the weight percentage of each component is: 80% of ground calcium carbonate, 6% of dispersant, 10% of carrier resin, 1% of cooling agent, 0.3% of antioxidant, toughening Agent 1.7%, coupling agent 1%.
[0020] Preparation method is the same as example 1.
Embodiment 3
[0022] An energy-saving, cooling and toughening filler masterbatch, the weight percentage of each component is: 70% of ground calcium carbonate, 8% of dispersant, 12% of carrier resin, 3% of cooling agent, 0.5% of antioxidant, toughening Agent 5%, coupling agent 1.5%.
[0023] Preparation method is the same as example 1.
PUM
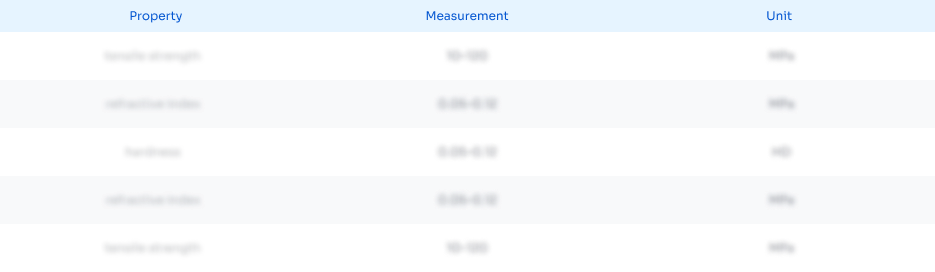
Abstract
Description
Claims
Application Information

- R&D
- Intellectual Property
- Life Sciences
- Materials
- Tech Scout
- Unparalleled Data Quality
- Higher Quality Content
- 60% Fewer Hallucinations
Browse by: Latest US Patents, China's latest patents, Technical Efficacy Thesaurus, Application Domain, Technology Topic, Popular Technical Reports.
© 2025 PatSnap. All rights reserved.Legal|Privacy policy|Modern Slavery Act Transparency Statement|Sitemap|About US| Contact US: help@patsnap.com