A self-emulsifying modified silicone resin emulsion and its preparation method and application
A resin emulsion and silicone technology, applied in the direction of resistor shell/packaging shell/potting, etc., can solve the problems of low strength and high baking temperature of silicone resin, and achieve the goal of reducing curing temperature, overcoming low strength and reducing emissions. Effect
- Summary
- Abstract
- Description
- Claims
- Application Information
AI Technical Summary
Problems solved by technology
Method used
Image
Examples
Embodiment 1
[0026] A method for preparing a self-emulsifying modified silicone resin emulsion of the present embodiment comprises the following steps:
[0027] (1) Add 11.73 parts by mass of polyester polyols containing sulfonic acid groups / carboxyl groups with a number average molecular weight of 733 to a reactor with a stirrer and a condensing reflux device. 2h, lower the temperature to 65°C, and control the stirring speed at 150rpm, add 7.54 parts by mass of 3-isocyanatopropyltrimethoxysilane (KH-901) into the reactor, raise the temperature to 75-80°C for 10 minutes, and then immediately Cool down to 60°C, add 8.9 parts by mass of methyltrimethoxysilane, 51.1 parts by mass of dimethyldimethoxysilane and 20 parts by mass of ethyl silicate, and continuously add 24.23 parts by mass of deionized water, the time for dropping for 0.5h, then raise the temperature to 90°C within 0.25h, keep it warm for 1h and then distill until no distillate is distilled out, then discharge the material after ...
Embodiment 2
[0032] A method for preparing a self-emulsifying modified silicone resin emulsion of the present embodiment comprises the following steps:
[0033] (1) Add 12.46 parts by mass of polyester polyols containing sulfonic acid groups / carboxyl groups with a number average molecular weight of 750 to a reactor with a stirrer and a condensing reflux device, and vacuumize and remove water for 2 hours at 130° C. Cool down to 70°C and control the stirring speed at 160rpm, add 8.27 parts by mass of 3-isocyanatopropyltrimethoxysilane (KH-901) into the reactor, raise the temperature to 80°C for 20 minutes and immediately cool down to 60°C, Add 23.14 parts by mass of methyltrimethoxysilane, 38.86 parts by mass of dimethyldimethoxysilane and 20 parts by mass of ethyl silicate, and continuously add 24.70 parts by mass of deionized water for 0.5 hours, and then Raise the temperature to 100°C within 0.3h, keep it warm for 1.5h, distill until no distillate is distilled, and discharge the material ...
Embodiment 3
[0038] A method for preparing a self-emulsifying modified silicone resin emulsion of the present embodiment comprises the following steps:
[0039] (1) Add 11.73 parts by mass of polyester polyols containing sulfonic acid groups / carboxyl groups with a number average molecular weight of 771 to a reactor with a stirrer and a condensing reflux device, and vacuumize and remove water for 2 hours at 130° C. Lower the temperature to 70°C and control the stirring speed to 170rpm, add 8.27 parts by mass of 3-isocyanatopropyltriethoxysilane (KH-907) into the reactor, raise the temperature to 80°C for 20 minutes and immediately cool down to 60°C , add 11.4 parts by mass of methyltriethoxysilane, 48.6 parts by mass of dimethyldiethoxysilane and 20 parts by mass of ethyl silicate, and continuously add 24.23 parts by mass of deionized water for 0.5h , then raise the temperature to 100°C within 0.25h, keep it warm for 1h, and then distill until no fraction is distilled out, and then discharg...
PUM
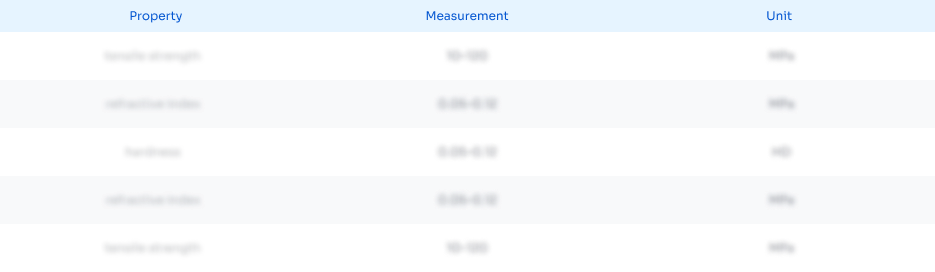
Abstract
Description
Claims
Application Information

- R&D
- Intellectual Property
- Life Sciences
- Materials
- Tech Scout
- Unparalleled Data Quality
- Higher Quality Content
- 60% Fewer Hallucinations
Browse by: Latest US Patents, China's latest patents, Technical Efficacy Thesaurus, Application Domain, Technology Topic, Popular Technical Reports.
© 2025 PatSnap. All rights reserved.Legal|Privacy policy|Modern Slavery Act Transparency Statement|Sitemap|About US| Contact US: help@patsnap.com