Ethanol, acetone and n-butanol salting-out composite rectification separation recovery method and apparatus
A rectification separation and n-butanol technology, applied in the separation/purification of hydroxyl compounds, carbonyl compounds, organic chemistry, etc., can solve the problem of low total solvent concentration, many impurities, and n-butanol in separation / water azeotrope and other problems, to achieve the effect of high solubility, good stability and easy recovery
- Summary
- Abstract
- Description
- Claims
- Application Information
AI Technical Summary
Problems solved by technology
Method used
Image
Examples
Embodiment 1
[0043] A salting-out composite rectification separation and recovery method for ethanol, acetone and n-butanol, comprising the steps of:
[0044] a) The cooked fermented mash is degassed (to remove CO 2 and H 2 ) after, it is sent into the beer tower 1 to carry out the concentration of the total solvent, and realize the separation of glucose, protein and solids etc. simultaneously. The composition of fermented mash is 95.0% water, 1.08% n-butanol, 0.54% acetone, 0.18% ethanol, and the rest are impurities such as glucose, protein and solids. After the fermented mash is preheated to a temperature of 85°C to 90°C, it is pumped into the middle of the mash tower 1 with a feed rate of 25,000kg / h. The bottom of the tower is heated by direct steam, and the pressure at the bottom of the tower is 2×10 4 ~3×10 4Pa, the temperature at the bottom of the tower is 106-108°C, the liquid level at the bottom of the tower is controlled at 1 / 2-2 / 3; the temperature at the top of the tower is 9...
Embodiment 2
[0051] A salting-out composite rectification separation and recovery method for ethanol, acetone and n-butanol, comprising the steps of:
[0052] a) The cooked fermented mash is degassed (to remove CO 2 and H 2 ) after, it is sent into the beer tower 1 to carry out the concentration of the total solvent, and realize the separation of glucose, protein and solids etc. simultaneously. The composition of fermented mash is 96.0% water, 1.08% n-butanol, 0.55% acetone, 0.17% ethanol, and the rest are impurities such as glucose, protein and solids. After the fermented mash is preheated to a temperature of 85°C to 90°C, it is pumped into the middle of the mash tower 1 with a feed rate of 25,000kg / h. The bottom of the tower is heated by direct steam, and the pressure at the bottom of the tower is 2×10 4 ~3×10 4 Pa, the temperature at the bottom of the tower is 106-108°C, the liquid level at the bottom of the tower is controlled at 1 / 2-2 / 3; the temperature at the top of the tower is ...
Embodiment 3
[0059] A salting-out composite rectification separation and recovery method for ethanol, acetone and n-butanol, comprising the steps of:
[0060] a) The cooked fermented mash is degassed (to remove CO 2 and H 2 ) after, it is sent into the beer tower 1 to carry out the concentration of the total solvent, and realize the separation of glucose, protein and solids etc. simultaneously. The composition of fermented mash is 94.0% water, 1.09% n-butanol, 0.54% acetone, 0.17% ethanol, and the rest are impurities such as glucose, protein and solids. After the fermented mash is preheated to a temperature of 85°C to 90°C, it is pumped into the middle of the mash tower 1 with a feed rate of 25,000kg / h. The bottom of the tower is heated by direct steam, and the pressure at the bottom of the tower is 2×10 4 ~3×10 4 Pa, the temperature at the bottom of the tower is 106-108°C, the liquid level at the bottom of the tower is controlled at 1 / 2-2 / 3; the temperature at the top of the tower is ...
PUM
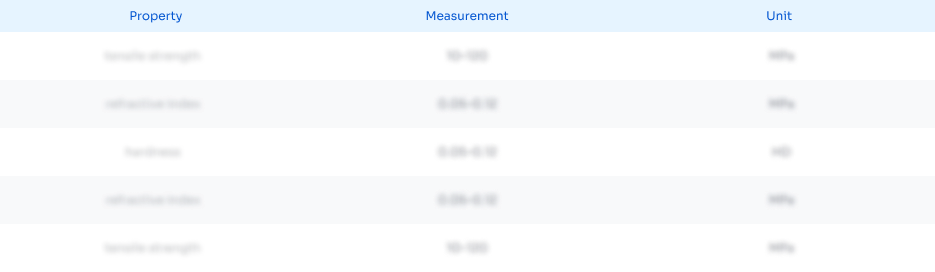
Abstract
Description
Claims
Application Information

- Generate Ideas
- Intellectual Property
- Life Sciences
- Materials
- Tech Scout
- Unparalleled Data Quality
- Higher Quality Content
- 60% Fewer Hallucinations
Browse by: Latest US Patents, China's latest patents, Technical Efficacy Thesaurus, Application Domain, Technology Topic, Popular Technical Reports.
© 2025 PatSnap. All rights reserved.Legal|Privacy policy|Modern Slavery Act Transparency Statement|Sitemap|About US| Contact US: help@patsnap.com