Machining technology facilitating improvement of nozzle machining efficiency
A technology of processing efficiency and processing technology, which is applied in the processing technology field of petroleum extraction equipment to achieve the effects of being beneficial to product quality, beneficial to quality, and reducing the amount of stripping
- Summary
- Abstract
- Description
- Claims
- Application Information
AI Technical Summary
Problems solved by technology
Method used
Examples
Embodiment 1
[0023] A processing technology that is beneficial to the processing efficiency of a nozzle, comprising the following steps:
[0024] A) blank forging;
[0025] B) heat treatment;
[0026] C) Machining;
[0027] The step C) is located before the step B), and the step C) includes mechanical roughing and mechanical semi-finishing sequentially performed on different lathes. In the step A), the material used for the blank is 45# steel, forged The temperature range is 875°C-1025°C, and the forging heat source adopts a reverberatory furnace; the step B) includes quenching and tempering after quenching;
[0028] Also included is a mechanical finishing step D) arranged after step B).
[0029] Specifically, the process of the present invention is simple. By selecting the material of the nozzle as 45# steel, and obtaining the optimal forging temperature range through a limited number of tests for the above-mentioned materials, the process of the present invention can select a low-cost...
Embodiment 2
[0032] This embodiment is further limited on the basis of Embodiment 1. In order to improve the plasticity of the blank and reduce the deformation resistance, the step A) further includes a step of preheating the blank before forging, and the step of preheating the blank is to be at room temperature The blank is heated to 200℃-350℃.
[0033] In order to obtain sufficient hardness, wear resistance and fatigue resistance of the nozzle and reduce the degree of oxidation of the surface of the nozzle during the quenching process, the quenching temperature range in the step B) is 820°C-850°C, and the quenching adopts the rapid cooling method of oil cooling. ;
[0034] In order to eliminate the internal stress generated in the nozzle during the quenching process, reduce the brittleness of the nozzle, improve the toughness of the nozzle, and reduce the degree of oxidation of the nozzle surface during the tempering process, the fiery temperature range of the tempering is 570℃-600℃, and...
PUM
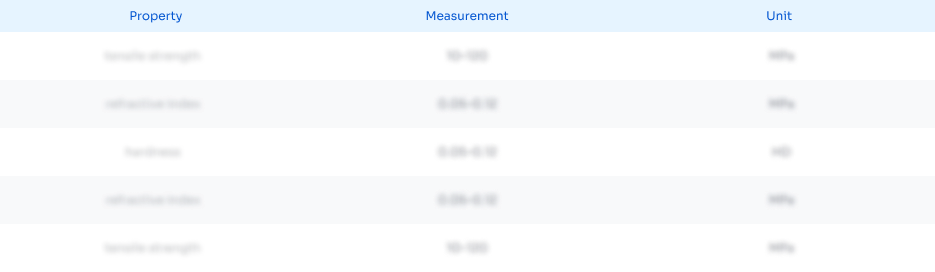
Abstract
Description
Claims
Application Information

- Generate Ideas
- Intellectual Property
- Life Sciences
- Materials
- Tech Scout
- Unparalleled Data Quality
- Higher Quality Content
- 60% Fewer Hallucinations
Browse by: Latest US Patents, China's latest patents, Technical Efficacy Thesaurus, Application Domain, Technology Topic, Popular Technical Reports.
© 2025 PatSnap. All rights reserved.Legal|Privacy policy|Modern Slavery Act Transparency Statement|Sitemap|About US| Contact US: help@patsnap.com