Preparation method of temperature responsive fiber for window curtain
A technology of temperature response and curtain, applied in the direction of fiber treatment, fiber chemical characteristics, spinning solution preparation, etc., to achieve the effect of good spinnability, simple method and obvious temperature response characteristics
- Summary
- Abstract
- Description
- Claims
- Application Information
AI Technical Summary
Problems solved by technology
Method used
Examples
Embodiment 1
[0032] (1) Pretreatment of PVDF powder. Prepare a sodium hydroxide solution with a molar ratio of 2mol / L, pour 350ml of the lye into a beaker, add 40g of white PVDF powder to the alkali solution, then add 5ml of absolute ethanol to the reaction system, and stir to make the PVDF Fully dispersed in the solution. The reaction system was placed in a constant temperature water bath at 50°C and reacted for 10 minutes. Suction filter the obtained product, and wash it continuously with distilled water to remove NaF and ethanol in the product, and finally put the powdery solid product obtained after washing into an oven at 60°C to dry for use.
[0033] (2) Preparation of thermosensitive copolymer. Take 10g of alkali-treated PVDF powder and put it into a three-necked flask, pass nitrogen gas, then add 120ml of solvent DMF, stir and dissolve in a water bath at 50°C under heating conditions. Take 10g of refined NIPAAm and 0.2g of initiator AIBN, and add them into a three-necked flask u...
Embodiment 2
[0038] (1) Pretreatment of PVDF powder. Prepare a potassium hydroxide solution with a molar ratio of 2mol / L, pour 350ml of the lye into a beaker, add 60g of white PVDF powder to the lye solution, then add 15ml of absolute ethanol to the reaction system, and stir to make the PVDF Fully dispersed in the solution. The reaction system was placed in a constant temperature water bath at 80°C and reacted for 20 minutes. The resulting product was suction filtered and washed continuously with distilled water to remove KF and ethanol in the product, and finally the powdery solid product obtained after washing was placed in an oven at 60°C to dry for use.
[0039] (2) Preparation of thermosensitive copolymer. Take 20g of alkali-treated PVDF powder and put it into a three-necked flask, pass nitrogen gas, then add 120ml of solvent DMF, stir and dissolve in a water bath at 80°C under heating conditions. Get 20g refined NIPAAm, 0.5g initiator AIBN, add in the three-necked flask under the ...
Embodiment 3
[0044] (1) Pretreatment of PVDF powder. Prepare a sodium hydroxide solution with a molar ratio of 2mol / L, pour 350ml of the lye into a beaker, add 50g of white PVDF powder to the alkali solution, then add 10ml of absolute ethanol to the reaction system, and stir to make the PVDF Fully dispersed in the solution. The reaction system was placed in a constant temperature water bath at 60°C and reacted for 20 minutes. Suction filter the obtained product, and wash it continuously with distilled water to remove NaF and ethanol in the product, and finally put the powdery solid product obtained after washing into an oven at 60°C to dry for use.
[0045] (2) Preparation of thermosensitive copolymer. Take 15g of alkali-treated PVDF powder and put it into a three-necked flask, pass nitrogen gas, then add 120ml of solvent DMF, stir and dissolve in a water bath at 60°C under heating conditions. Take 15g of refined NIPAAm and 0.2g of initiator AIBN, and add them into a three-necked flask ...
PUM
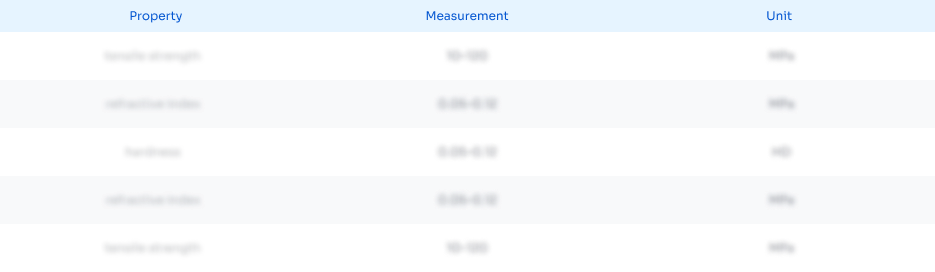
Abstract
Description
Claims
Application Information

- Generate Ideas
- Intellectual Property
- Life Sciences
- Materials
- Tech Scout
- Unparalleled Data Quality
- Higher Quality Content
- 60% Fewer Hallucinations
Browse by: Latest US Patents, China's latest patents, Technical Efficacy Thesaurus, Application Domain, Technology Topic, Popular Technical Reports.
© 2025 PatSnap. All rights reserved.Legal|Privacy policy|Modern Slavery Act Transparency Statement|Sitemap|About US| Contact US: help@patsnap.com