Process for recovering zinc from tin-smelting electric furnace smoke
A technology for soot and electric furnace, applied in the field of comprehensive recovery of non-ferrous metal resources, can solve the problems of direct tin yield, increase in production cost, pollution of resources, loss, etc., and achieve the effects of increased yield, reduced production cost and easy operation.
- Summary
- Abstract
- Description
- Claims
- Application Information
AI Technical Summary
Problems solved by technology
Method used
Image
Examples
Embodiment 1
[0033] Collect 0.5t of high-zinc-tin smoke dust produced in the electric furnace tin smelting, and the zinc-containing rate is 20% after testing. Add water with a solid-to-liquid volume ratio of 2 to 4 times, adjust the pH value to 4 to 6 with a pH adjusting solution, extract at a temperature of 80 to 90°C for 0.5 to 1 hour, and filter to obtain filtrate a; Inorganic acid leaching solution with a liquid volume ratio of 2 to 4 times and a pH value of 1 to 2 is extracted at a temperature of 80 to 90°C for 0.5 to 1 hour, and filtrate b is obtained by filtration; filtrate a and filtrate b are combined, and sodium carbonate is added to adjust the pH to 5 ~7, hydrolyze at a temperature of 50~70°C for 0.5~1h, and filter; the filter residue after hydrolysis and filtration is leached at a temperature of 80~90°C with an inorganic acid leach solution with a pH value of 1~2 and a solid-to-liquid volume ratio of 2~4 times After extracting for 0.5~1h and filtering, 420 Kg of tin slag was ob...
Embodiment 2
[0035] Collect 1 ton of high-zinc-tin fumes produced in electric furnace tin smelting, and the zinc content rate is 30% after testing. Add water with a solid-to-liquid volume ratio of 2 to 4 times, adjust the pH value to 4 to 6 with a pH adjusting solution, extract at a temperature of 80 to 90°C for 0.5 to 1 hour, and filter to obtain filtrate a; Inorganic acid leaching solution with a liquid volume ratio of 2 to 4 times and a pH value of 1 to 2 is extracted at a temperature of 80 to 90°C for 0.5 to 1 hour, and filtrate b is obtained by filtration; filtrate a and filtrate b are combined, and sodium carbonate is added to adjust the pH to 5 ~7, hydrolyze at a temperature of 50~70°C for 0.5~1h, and filter; the filter residue after hydrolysis and filtration is leached at a temperature of 80~90°C with an inorganic acid leach solution with a pH value of 1~2 and a solid-to-liquid volume ratio of 2~4 times After extracting for 0.5~1h and filtering, 709 Kg of tin slag was obtained and ...
Embodiment 3
[0037] 2 t of high-zinc-tin fume generated in electric furnace tin smelting was collected, and the zinc content rate was 25% after testing. Add water with a solid-to-liquid volume ratio of 2 to 4 times, adjust the pH value to 4 to 6 with a pH adjusting solution, extract at a temperature of 80 to 90°C for 0.5 to 1 hour, and filter to obtain filtrate a; Inorganic acid leaching solution with a liquid volume ratio of 2 to 4 times and a pH value of 1 to 2 is extracted at a temperature of 80 to 90°C for 0.5 to 1 hour, and filtrate b is obtained by filtration; filtrate a and filtrate b are combined, and sodium carbonate is added to adjust the pH to 5 ~7, hydrolyze at a temperature of 50~70°C for 0.5~1h, and filter; the filter residue after hydrolysis and filtration is leached at a temperature of 80~90°C with an inorganic acid leach solution with a pH value of 1~2 and a solid-to-liquid volume ratio of 2~4 times After extracting for 0.5~1h and filtering, 1515Kg of tin slag is obtained ...
PUM
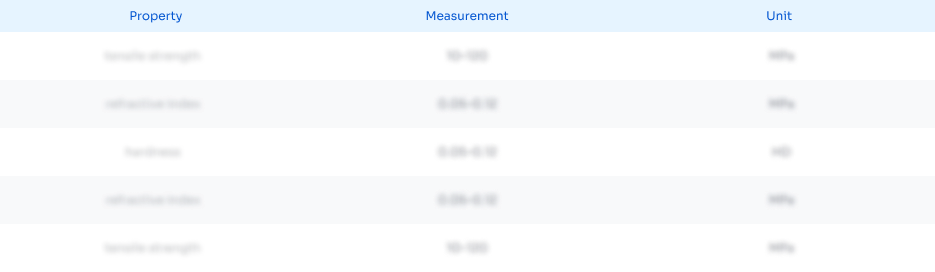
Abstract
Description
Claims
Application Information

- R&D
- Intellectual Property
- Life Sciences
- Materials
- Tech Scout
- Unparalleled Data Quality
- Higher Quality Content
- 60% Fewer Hallucinations
Browse by: Latest US Patents, China's latest patents, Technical Efficacy Thesaurus, Application Domain, Technology Topic, Popular Technical Reports.
© 2025 PatSnap. All rights reserved.Legal|Privacy policy|Modern Slavery Act Transparency Statement|Sitemap|About US| Contact US: help@patsnap.com