Method for preparing ultramarine blue pigment
A pigment and Qunlan technology, which is applied in the direction of inorganic pigment treatment, chemical instruments and methods, fibrous fillers, etc., can solve the problems of long production cycle, high energy consumption, and high impurity content of Qunlan products, and achieve short reaction cycle and weather resistance Good performance and bright colors
- Summary
- Abstract
- Description
- Claims
- Application Information
AI Technical Summary
Problems solved by technology
Method used
Image
Examples
Embodiment 1
[0042] Na 2 CO 3 , elemental sulfur, sodium hydroxide and activated carbon were dried at 110°C for 1 hour, and NaA molecular sieve was dried at 500°C for 1 hour; weigh 500 grams of NaA molecular sieve, 100 grams of elemental sulfur, 120 grams of sodium carbonate, and 5 grams, 25 grams of activated carbon, ground and mixed, placed in a ceramic crucible, compacted and sealed. Place the sealed crucible in an electric furnace, raise it to 600°C at a rate of 15°C / min for the first-stage calcination, and keep the temperature constant for 90 minutes to obtain a green solid. Fill the crucible with oxygen, carry out the second-stage roasting at 500°C, and keep the temperature constant for 40 minutes to obtain the crude group blue product. The prepared crude product was repeatedly washed in water at 60°C to remove water-soluble salts, and the crude product of Qunlan blue pigment after washing was stirred in 2% and 100°C sodium sulfite solution (solid-to-liquid ratio was 1:2) for 5 min...
Embodiment 2
[0044] Na 2 CO 3 , elemental sulfur, sodium hydroxide and activated carbon were dried at 110°C for 1 hour, and NaA molecular sieve was dried at 500°C for 1 hour; weigh 500 grams of NaA molecular sieve, 240 grams of elemental sulfur, 90 grams of sodium carbonate, and 35 grams, 80 grams of activated carbon, ground and mixed, placed in a ceramic crucible, compacted and sealed. Place the sealed crucible in an electric furnace, raise it to 750°C at a rate of 5°C / min for the first-stage calcination, and keep the temperature constant for 30 minutes to obtain a green solid. Fill the crucible with oxygen, carry out the second-stage calcination at 400°C, and keep the temperature constant for 80 minutes to obtain the crude group blue product. The prepared crude product was repeatedly washed in 100°C water to remove water-soluble salts, and the washed Qunlan blue pigment was stirred in 4% hot sodium sulfite solution at 80°C (solid-to-liquid ratio 1:3) for 6 minutes, washed with water, a...
Embodiment 3
[0046] Na 2 CO 3 , elemental sulfur, sodium hydroxide and rosin were dried at 110°C for 1 hour, and NaA molecular sieve was dried at 500°C for 1 hour; weigh 500 grams of NaA molecular sieve, 170 grams of elemental sulfur, 65 grams of sodium carbonate, and 20 grams of sodium hydroxide gram, 50 grams of rosin, ground and mixed, placed in a ceramic crucible, compacted and sealed. Put the sealed crucible in an electric furnace, raise it to 700°C at a rate of 10°C / min for the first-stage calcination, and keep the temperature constant for 60 minutes to obtain a green solid. Fill the crucible with oxygen, carry out the second-stage roasting at 450°C, and keep the temperature constant for 60 minutes to obtain the crude group blue product. The prepared product was repeatedly washed in water at 80°C to remove water-soluble salts, and the washed Qunlan blue pigment was stirred in 3% hot sodium sulfite solution at 60°C (solid-to-liquid ratio of 1:4) for 10 minutes, washed with water, an...
PUM
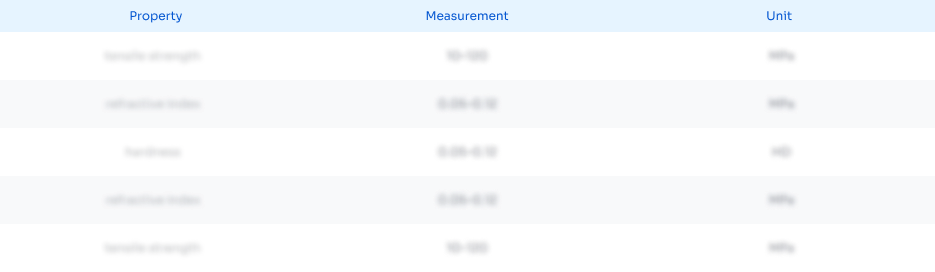
Abstract
Description
Claims
Application Information

- R&D Engineer
- R&D Manager
- IP Professional
- Industry Leading Data Capabilities
- Powerful AI technology
- Patent DNA Extraction
Browse by: Latest US Patents, China's latest patents, Technical Efficacy Thesaurus, Application Domain, Technology Topic, Popular Technical Reports.
© 2024 PatSnap. All rights reserved.Legal|Privacy policy|Modern Slavery Act Transparency Statement|Sitemap|About US| Contact US: help@patsnap.com