Miniature active matrix type organic light emitting display and manufacturing method thereof
A light-emitting display and matrix technology, applied in the field of miniature active-matrix organic light-emitting display and its production, can solve problems such as increased manufacturing difficulty, and achieve the effect of high reliability
- Summary
- Abstract
- Description
- Claims
- Application Information
AI Technical Summary
Problems solved by technology
Method used
Image
Examples
Embodiment 1
[0032] Such as Figure 4 shown.
[0033] A miniature active matrix organic light-emitting display, which mainly consists of a silicon wafer substrate 1, a pixel electrode 2, an insulating layer 3 (made of polyimide), a hole injection layer 4, a hole transport layer 5, a light-emitting layer 6, and an excitation layer. Sub barrier layer 7, electron transport layer 8, electron injection layer 9, cathode motor layer 10, sealing layer I11, sealing layer II12, sealing layer III13, color photoresist layer 14, black matrix layer 15 and glass substrate 16. A plurality of anode pixel electrodes 2 are made on the silicon substrate 1, and the material of the anode pixel electrodes 2 is a single-layer material or a multi-layer composite material, the single-layer material is Al, Mo or W, and the composite material is Mo / Al / Mo, Al / Mo, Cr / Al / Mo or Cr / Ti / Al / Mo, the total thickness of the anode pixel electrode 2 is between 60nm and 550nm, and the anode pixel electrode 15 is patterned to for...
Embodiment 2
[0035] Such as figure 1 , 3 shown.
[0036] A method for manufacturing a micro-active matrix organic light-emitting display includes manufacturing an anode pixel electrode on a silicon wafer substrate, manufacturing an OLED device layer on the anode electrode, manufacturing a thin film sealing layer for encapsulating an OLED structure, and manufacturing a color pixel electrode on a glass substrate. Fabrication of filter layer and black matrix, glue coating on silicon substrate and lamination with glass substrate. Specific steps are as follows:
[0037] (1) Fabrication of anode pixel electrodes; the process is: silicon wafer substrate cleaning, deposition of anode electrodes by sputtering or electron beam evaporation, and patterning of anode pixel electrodes by dry etching, with a pixel area of (3 μm to 5 μm )×(9μm~15μm). Such as figure 1 shown
[0038] The materials used for the anode pixel electrode are single-layer materials such as Al, Mo, W, etc., and also in...
example 1
[0047] The invention provides a preparation method for realizing a high-resolution color micro AMOLED display. An AMOLED display includes an anode, a cathode, and a light-emitting layer sandwiched in between. The resolution of the micro AMOLED display is determined by the pattern accuracy of the anode. The invention provides a feasible high-precision anode preparation scheme. refer to figure 1 , first deposit the anode film on the silicon substrate. The anode material is required to be electrically compatible with the silicon substrate and the OLED light-emitting layer. You can choose to use single-layer materials such as Al, Mo, W, or Mo / Al / Mo , Al / Mo, Cr / Al / Mo, Cr / Ti / Al / Mo and other multi-layer material structures, the total thickness of the electrode is between 60nm and 250nm.
[0048] Secondly, in order to achieve high patterning accuracy, plasma dry etching is chosen for patterning. Furthermore, methods such as laser etching can also be selected to realize anode patte...
PUM
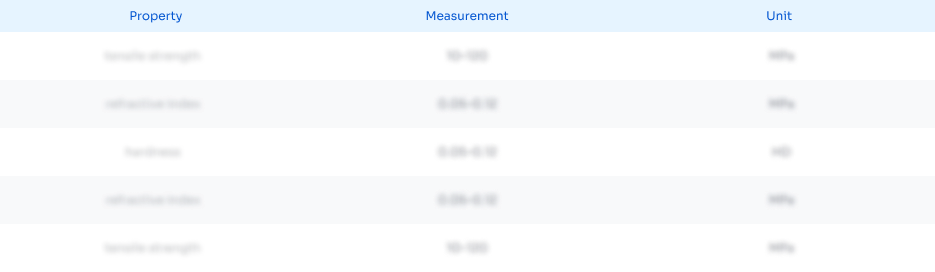
Abstract
Description
Claims
Application Information

- Generate Ideas
- Intellectual Property
- Life Sciences
- Materials
- Tech Scout
- Unparalleled Data Quality
- Higher Quality Content
- 60% Fewer Hallucinations
Browse by: Latest US Patents, China's latest patents, Technical Efficacy Thesaurus, Application Domain, Technology Topic, Popular Technical Reports.
© 2025 PatSnap. All rights reserved.Legal|Privacy policy|Modern Slavery Act Transparency Statement|Sitemap|About US| Contact US: help@patsnap.com