Reaction sintered ceramic bulletproof insert plate and preparation method of reaction sintered bulletproof ceramic
A technology of bulletproof inserts and sintered ceramics, which is applied in the field of inorganic non-metallic materials, can solve problems such as difficult removal, product performance degradation, and difficulty in residual silicon, so as to reduce labor intensity, facilitate industrialized large-scale production, and realize industrialized large-scale production Effect
- Summary
- Abstract
- Description
- Claims
- Application Information
AI Technical Summary
Problems solved by technology
Method used
Image
Examples
Embodiment 1
[0021] 1) Mix the raw materials whose mass composition is 90% of silicon carbide powder, 3% of carbon black powder, and 7% of polyvinyl alcohol, spray dry and granulate, and then press and form in a mold to obtain a silicon carbide compact, Such as figure 1 , figure 2 shown;
[0022] 2) After mixing the mass composition of 70% silicon powder, 5% silicon carbide powder and 25% boron nitride powder evenly, press and form in a mold to obtain a compact of sintered infiltration agent;
[0023] 3) Stack the silicon carbide compact and the infiltration agent compact together in a vacuum of 4×10 -1 In a Pa vacuum furnace, heat up to 1550°C for sintering and heat preservation for 1 hour to obtain reaction sintered silicon carbide;
[0024] 4) Tapping and removing the infiltrating agent residue on the surface of the sintered silicon carbide to obtain a reaction sintered silicon carbide ceramic chip.
[0025] Such as image 3 As shown, a bulletproof board made of reaction sintered ...
Embodiment 2
[0027] 1) After mixing the raw materials whose mass composition is 85% of boron carbide powder, 5% of carbon black powder, and 10% of paraffin wax solution, they are spray-dried and granulated, and then pressed into a mold to obtain a boron carbide compact;
[0028] 2) After mixing the mass composition of 65% silicon powder, 3% silicon carbide powder and 32% boron nitride powder evenly, press and form in a mold to obtain a compact of sintered infiltration agent;
[0029] 3) Stack boron carbide compacts and infiltration agent compacts together in a vacuum of 1×10 -1 In a Pa vacuum furnace, heat up to 1550°C for sintering and heat preservation for 1 hour to obtain reaction sintered boron carbide;
[0030] 4) Tapping and removing the infiltrating agent residue on the surface of the sintered boron carbide to obtain a reaction sintered boron carbide ceramic chip.
Embodiment 3
[0032] 1) After mixing the raw materials whose mass composition is 80% of silicon carbide powder, 10% of carbon black powder, and 10% of phenolic resin solution, they are spray-dried and granulated, and then pressed into a mold to obtain a silicon carbide compact;
[0033] 2) After mixing the mass composition of 70% silicon powder, 8% silicon carbide powder and 22% boron nitride powder evenly, press and form in a mold to obtain a compact of sintered infiltration agent;
[0034] 3) Stack the silicon carbide compact and the infiltration agent compact together in a vacuum of 3×10 -1 In a Pa vacuum furnace, heat up to 1650°C for sintering and heat preservation for 3 hours to obtain reaction sintered silicon carbide;
[0035] 4) Tapping and removing the infiltrating agent residue on the surface of the sintered silicon carbide to obtain a reaction sintered silicon carbide ceramic chip.
PUM
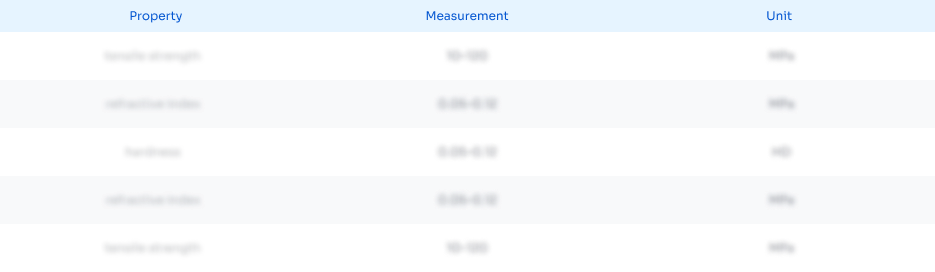
Abstract
Description
Claims
Application Information

- R&D
- Intellectual Property
- Life Sciences
- Materials
- Tech Scout
- Unparalleled Data Quality
- Higher Quality Content
- 60% Fewer Hallucinations
Browse by: Latest US Patents, China's latest patents, Technical Efficacy Thesaurus, Application Domain, Technology Topic, Popular Technical Reports.
© 2025 PatSnap. All rights reserved.Legal|Privacy policy|Modern Slavery Act Transparency Statement|Sitemap|About US| Contact US: help@patsnap.com