Manufacturing process of cupronickel pipe
A manufacturing process, white copper tube technology, applied in the field of white copper tube manufacturing process, can solve the problems of low yield, pollution, high energy consumption, etc., achieve significant economic benefits, simplify the process flow, and reduce energy consumption.
- Summary
- Abstract
- Description
- Claims
- Application Information
AI Technical Summary
Problems solved by technology
Method used
Examples
Embodiment 1
[0008] Embodiment 1. Production of Φ25×0.75×8000BFe10-1-1 white copper tube. Continuously add electrolytic copper and electrolytic nickel plates, appropriate amount of pure iron blocks, and electrolytic manganese blocks into the continuous melting furnace for melting. The final alloy melt test ratio continues to meet the requirements of the national standard CB / T5231-2001 for BFe10-1-1 cupronickel material: Ni+Co / 9.0~11.0%, Fe / 1.0~1.5%, Mn / 0.5~1.0% , the impurity content does not exceed 0.7%, and the rest is Cu. The cupronickel alloy melt that reaches the qualified composition enters the holding furnace through the connecting channel for heat preservation, and then enters the continuous crystallizer for casting and crystallization. The cooling water pressure of the continuous crystallizer is controlled between 0.2-0.8MPa During the period, after the melt of copper-nickel matrix copper-nickel alloy is continuously crystallized, a Φ45×3.5 white copper tube billet is continuously...
Embodiment 2
[0009] Embodiment 2. Production of Φ40×1.5×6000B30 white copper tube. Continuously add electrolytic copper and electrolytic nickel plates, appropriate amount of pure iron blocks, and electrolytic manganese blocks into the continuous melting furnace for melting. The final alloy melt test ratio continues to meet the B30 white copper material requirements stipulated in the national standard CB / T5231-2001: that is, Ni+Co / 29~33%, Fe / 0.9%, Mn / 1.2%, and the rest is Cu, reaching the qualified composition The white copper alloy melt enters the holding furnace through the connecting channel for heat preservation, and then enters the continuous crystallizer for casting and crystallization. The cooling water pressure of the continuous mold is controlled between 0.2 and 0.8MPa. The double-roller extrusion of the casting machine continuously pulls out the Φ70×4 white copper tube blank upwards, the pulling speed is 80mm / min, and the length of each section of the tube blank is 5mm. machine, ...
PUM
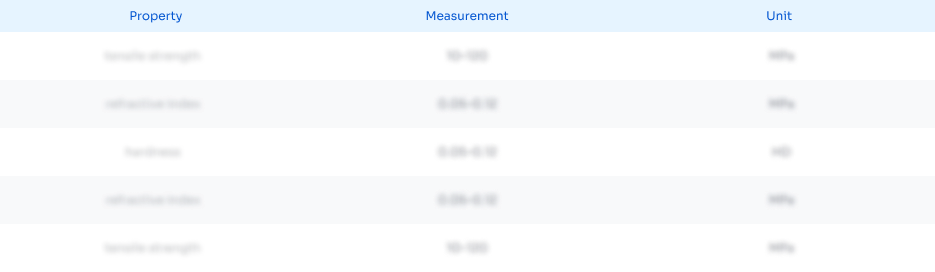
Abstract
Description
Claims
Application Information

- Generate Ideas
- Intellectual Property
- Life Sciences
- Materials
- Tech Scout
- Unparalleled Data Quality
- Higher Quality Content
- 60% Fewer Hallucinations
Browse by: Latest US Patents, China's latest patents, Technical Efficacy Thesaurus, Application Domain, Technology Topic, Popular Technical Reports.
© 2025 PatSnap. All rights reserved.Legal|Privacy policy|Modern Slavery Act Transparency Statement|Sitemap|About US| Contact US: help@patsnap.com