Extruder unit
An extrusion unit and extruder technology, applied in the field of extrusion units, can solve problems such as high extrusion pressure, low work efficiency, and poor product quality, and achieve the effects of enhanced sealing performance, increased efficiency, and guaranteed quality
- Summary
- Abstract
- Description
- Claims
- Application Information
AI Technical Summary
Problems solved by technology
Method used
Image
Examples
Embodiment Construction
[0018] Such as figure 1 , figure 2 As shown, it is an extruder unit disclosed by the present invention, including a first extruder, in which a heating zone, a melting zone, a kneading zone, a screen changer, and a static mixer are sequentially arranged in the first extruder. The outlet of the static mixer communicates with the inlet of the melt pump through a pipeline, and the outlet of the melt pump communicates with the feeding port of the second extruder through a pipeline. The heating system is divided into heating zone, melting zone and mixing zone. The heating zone, melting zone and mixing zone are all heated by electric heaters. The heaters use cast aluminum heaters with cooling air ducts. The heating power of each heater Generally 2-3KW, preferably 2.5KW. The cooling air channel and the cooling system are kept unobstructed. The cooling system adopts air cooling, and an AC motor is used to drive a centrifugal fan as the air source. The power of the fan is generally 2...
PUM
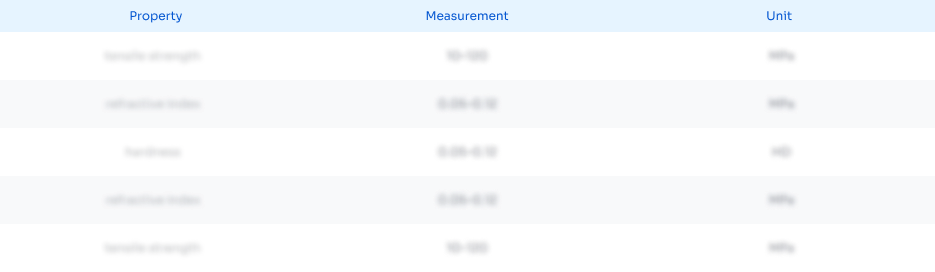
Abstract
Description
Claims
Application Information

- R&D Engineer
- R&D Manager
- IP Professional
- Industry Leading Data Capabilities
- Powerful AI technology
- Patent DNA Extraction
Browse by: Latest US Patents, China's latest patents, Technical Efficacy Thesaurus, Application Domain, Technology Topic, Popular Technical Reports.
© 2024 PatSnap. All rights reserved.Legal|Privacy policy|Modern Slavery Act Transparency Statement|Sitemap|About US| Contact US: help@patsnap.com