Preparation method of composite oxide AB2O4 for lithium ion secondary battery cathode material
A composite oxide, AB2O4 technology, applied in the field of preparation of composite oxide AB2O4 for lithium-ion secondary battery negative electrode materials, can solve the problems of small diffusion coefficient of lithium ions, short circuit of lithium dendrites, electrolyte consumption and other problems, and achieve improvement The effects of electrochemical performance, increased specific surface area, and simple preparation process
- Summary
- Abstract
- Description
- Claims
- Application Information
AI Technical Summary
Problems solved by technology
Method used
Image
Examples
Embodiment 1
[0022] Dissolve cobalt acetate and nickel acetate in deionized water at a molar ratio of 0.01 mol: 0.005 mol; Wet with ionic water, add 0.15 mol (12 mL) ammonia water, shake until a colorless and transparent solution is formed, then add the colorless and transparent double chelating agent EDTA-PPA solution into the saline solution to form a transparent solution, heat and stir at 80°C until a gelatinous solution is formed. glue. (3) Pre-freeze the gel material in a freezer at -80°C for 1 h; (4) Transfer the pre-frozen material into a freeze-drying device and vacuum freeze-dry for 2 days. (5) Transfer the freeze-dried material into a muffle furnace and calcinate at 650 °C for 5 h with a heating rate of 5 °C / min.
[0023] figure 1 It is the SEM picture of the material, it can be seen from the picture that the particle size distribution of the material is relatively uniform, and the particle size is about 100 nm; figure 2 It is the electrochemical performance diagram of the ma...
Embodiment 2
[0025] Dissolve cobalt nitrate and zinc nitrate in deionized water at a molar ratio of 0.01 mol: 0.005 mol; Wet with ionic water, add 0.15 mol (12 mL) ammonia water, shake until a colorless and transparent solution is formed, then add the colorless and transparent double chelating agent EDTA-CA solution into the saline solution to form a transparent solution, heat and stir at 70°C until a gelatinous solution is formed. glue. (3) Pre-freeze the gel material in a freezer at -20°C for 1 h; (4) Transfer the pre-frozen material into a freeze-drying device and vacuum freeze-dry for 1 day. (5) The freeze-dried material was transferred into a muffle furnace and calcined at 600 °C for 5 h with a heating rate of 2 °C / min.
[0026]
Embodiment 3
[0028] Dissolve manganese acetate and cobalt acetate in deionized water at a molar ratio of 0.01 mol: 0.005 mol; Wet with ionic water, add 0.15 mol (12 mL) ammonia water, shake until a colorless and transparent solution is formed, then add the colorless and transparent double chelating agent EDTA-CA solution into the saline solution to form a transparent solution, heat and stir at 70°C until a gelatinous solution is formed. glue. (3) Pre-freeze the gel material in a freezer at -20°C for 1 h; (4) Transfer the pre-frozen material into a freeze-drying device and vacuum freeze-dry for 1 day. (5) Transfer the freeze-dried material into a muffle furnace and calcinate at 600 °C for 5 h with a heating rate of 2 °C / min.
PUM
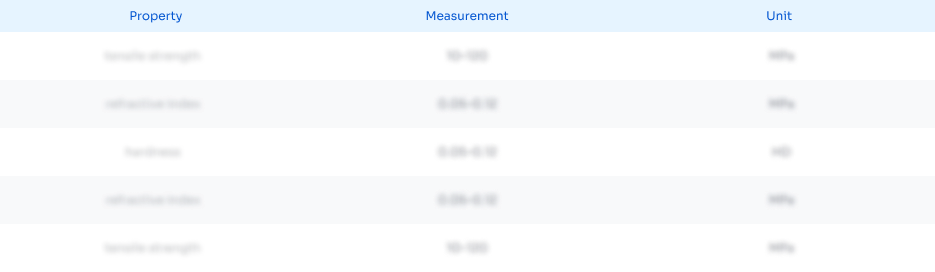
Abstract
Description
Claims
Application Information

- R&D
- Intellectual Property
- Life Sciences
- Materials
- Tech Scout
- Unparalleled Data Quality
- Higher Quality Content
- 60% Fewer Hallucinations
Browse by: Latest US Patents, China's latest patents, Technical Efficacy Thesaurus, Application Domain, Technology Topic, Popular Technical Reports.
© 2025 PatSnap. All rights reserved.Legal|Privacy policy|Modern Slavery Act Transparency Statement|Sitemap|About US| Contact US: help@patsnap.com