Coal pretreatment method for coal electrolysis hydrogenation liquefaction
A technology for hydroliquefaction and pretreatment, applied in electrolysis components, electrolysis process, electrolysis organic production, etc., can solve the problems of energy waste, high requirements on equipment and equipment, and achieve higher liquefaction yield, larger specific surface area, and higher current density. Effect
- Summary
- Abstract
- Description
- Claims
- Application Information
AI Technical Summary
Problems solved by technology
Method used
Image
Examples
Embodiment 1
[0021] 1 Coal pre-treatment process before irradiation: First, the coal is ball-milled in a ball mill at 80 rpm for 5 hours, and then filtered through a 200-mesh sieve to obtain finer coal particles with a coal particle size of about 50 μm.
[0022] 2 Pretreatment process of irradiated bottles: Clean irradiated bottles, rubber stoppers and gaskets according to the following process: detergent-water-deionized water-ultrapure water, wash 3 times, and then put the bottle in a vacuum drying oven Dry at 70 degrees inside, and put the rubber plug and gasket in an air-conditioned room to dry to prevent the rubber plug from heating and oxidation.
[0023] 3 Sample encapsulation process: Put 2g of coal sample into the irradiation bottle, and at the same time, use a pipette gun to transfer 10%H 2 o 2 Solution (oxidant) 5mL, first cover the bottle mouth with a plastic gasket, then compact it with a rubber stopper without leaving any gaps, and finally seal it with an aluminum cap with...
Embodiment 2
[0027] The rest of the steps in this example are the same as in Example 1, only step 3 has the following changes, namely:
[0028] Sample encapsulation process: put 2g of coal sample into the irradiation bottle, and at the same time transfer 5mL of ultrapure water with a pipette gun, first cover the mouth of the bottle with a plastic gasket, then compact it with a rubber stopper without leaving any gaps, and finally use it with an aluminum cap. Seal with sealing pliers. Finally get the pure water-coal irradiation sample
Embodiment 3
[0030] The rest of the steps in this example are the same as in Example 1, only step 3 has the following changes, namely:
[0031] Sample encapsulation process: first dehydrate 2g of coal in a vacuum drying oven at a vacuum degree of 0.05MPa and a temperature of 110°C for 24 hours, then put the sample into an irradiation bottle, first cover the mouth of the bottle with a plastic gasket, and then compact it with a rubber stopper Leave no gaps, and finally seal the aluminum lid with sealing pliers. The dry coal irradiated sample is finally obtained as dry coal (without any liquid added).
[0032] For the analysis of coal elements before and after irradiation treatment, see Table 1.
[0033]
[0034] Table 1 Elemental analysis of coal samples before and after irradiation treatment
[0035] C (wt. %) H (wt. %) H / C (at. %) dry coal 70.593 4.856 0.82 Irradiated dry coal 66.331 5.179 0.937 Irradiated dry coal + hydrogen peroxide 51.254 5.38...
PUM
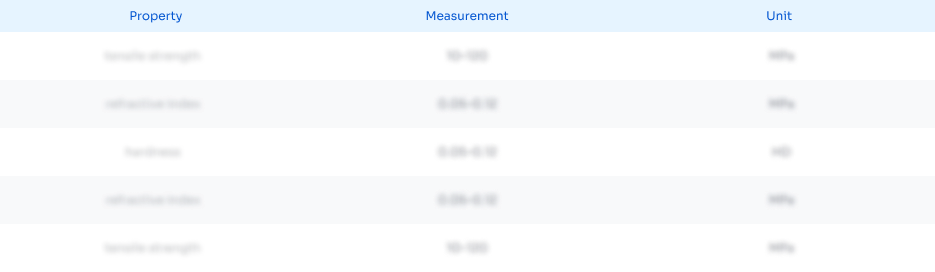
Abstract
Description
Claims
Application Information

- R&D
- Intellectual Property
- Life Sciences
- Materials
- Tech Scout
- Unparalleled Data Quality
- Higher Quality Content
- 60% Fewer Hallucinations
Browse by: Latest US Patents, China's latest patents, Technical Efficacy Thesaurus, Application Domain, Technology Topic, Popular Technical Reports.
© 2025 PatSnap. All rights reserved.Legal|Privacy policy|Modern Slavery Act Transparency Statement|Sitemap|About US| Contact US: help@patsnap.com