Preparation method for synthesis of ethyl 3-ethoxypropionate
A technology of ethyl ethoxy propionate and ethyl acrylate, applied in the field of preparation of synthesizing ethyl 3-ethoxy propionate, can solve the difficulty of increasing separation steps, increasing side reactions, and increasing organic salts to purify products And other issues
- Summary
- Abstract
- Description
- Claims
- Application Information
AI Technical Summary
Problems solved by technology
Method used
Image
Examples
specific Embodiment 1
[0047] Specific Example 1: In a fixed-bed reactor with a radius of 2.5 centimeters and a height of 75 centimeters, the catalyst is fixed inside, and the catalyst is first cleaned with absolute ethanol, then purged with nitrogen, then washed with deionized water, and then again Purged with nitrogen, then treated with 2-10% lye, washed with water after treatment, then filled with nitrogen, then washed with fresh ethanol or a mixture of ethanol and ethyl acrylate under nitrogen, and then filled with nitrogen Wash with ethanol until the water content of the cleaned ethanol in the system is not more than 0.1%. In the batching tank, the mass ratio of absolute ethanol and ethyl acrylate is 85:15, and the catalyst is about 15% of ethyl acrylate. Cool to The temperature is between 9-13 degrees, and it is passed into the fixed bed reactor according to the dilution rate of 2.1. The temperature of the reactor is controlled at 26±2 degrees. The material in the tank is rectified through the...
specific Embodiment 2
[0048]Specific embodiment 2: on the fixed-bed reactor surface of above embodiment 1, fix catalyst, clean and dry as embodiment 1, be 85:15 by the mass ratio of dehydrated alcohol and ethyl acrylate in batching tank, catalyst It is about 15% of ethyl acrylate, cooled to a temperature between 19-20 degrees, passed into a fixed bed reactor at a dilution rate of 2.0, the temperature of the reactor is controlled at 28±2 degrees, and the reacted material enters the receiving tank , measure the content of ethyl acrylate inside, the material in the receiving tank is rectified by the rectification tower, the EEP with a purity of 99% is collected as the product, and the yield is calculated, the excess ethanol and unreacted ethyl acrylate and a small amount of entrainment Return EEP to the batching tank and add fresh absolute ethanol and ethyl acrylate to adjust to 85:15, and enter the fixed bed circulation reaction. After continuous operation for 105 hours, 0.3% of ethyl acrylate discha...
specific Embodiment 3
[0049] Specific embodiment 3: on the fixed-bed reactor surface of above embodiment 1, fix catalyst, clean and dry as embodiment 1, be 85:15 by the mass ratio of dehydrated alcohol and ethyl acrylate in batching tank, catalyst It is about 15% of ethyl acrylate, cooled to a temperature between 13-15 degrees, passed into a fixed bed reactor at a dilution rate of 2.0, the temperature of the reactor is controlled at 28±2 degrees, and the reacted material enters the receiving tank , measure the content of ethyl acrylate inside, the material in the receiving tank is rectified by the rectification tower, the EEP with a purity of 99% is collected as the product, and the yield is calculated, the excess ethanol and unreacted ethyl acrylate and a small amount of entrainment Return EEP to the batching tank and add fresh absolute ethanol and ethyl acrylate to adjust to 85:15, and enter the fixed bed circulation reaction. After continuous operation for 90 hours, 0.8% of ethyl acrylate discha...
PUM
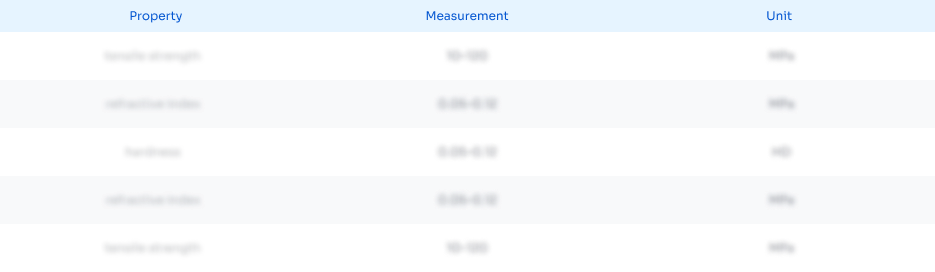
Abstract
Description
Claims
Application Information

- R&D
- Intellectual Property
- Life Sciences
- Materials
- Tech Scout
- Unparalleled Data Quality
- Higher Quality Content
- 60% Fewer Hallucinations
Browse by: Latest US Patents, China's latest patents, Technical Efficacy Thesaurus, Application Domain, Technology Topic, Popular Technical Reports.
© 2025 PatSnap. All rights reserved.Legal|Privacy policy|Modern Slavery Act Transparency Statement|Sitemap|About US| Contact US: help@patsnap.com