Low-sulfur large-grained salt produced from sodium sulfate type salt mine and preparation method thereof
A sodium sulfate, large-grain technology, applied in the direction of calcium/strontium/barium halides, alkali metal chlorides, calcium/strontium/barium chlorides, etc., can solve the problem of small footprint, short process flow, and no multiple effects Evaporate salt production process and other issues to achieve the effect of reducing waste residue discharge, saving electric energy and increasing sales radius
- Summary
- Abstract
- Description
- Claims
- Application Information
AI Technical Summary
Problems solved by technology
Method used
Image
Examples
preparation example Construction
[0057] The preparation process of low-sulfur large-grain salt includes: mixing ammonia-soda waste liquid with water and injecting it into sodium sulfate type salt mine for underground desulfurization, producing calcium chloride content of 40-120g / L and magnesium content of 0g / L, calcium sulfate content 0.2 ~ 1.5g / L, high calcium brine saturated with sodium chloride. The calcium chloride content of the high-calcium brine is preferably 50-115 g / L, more preferably 60-110 g / L, and most preferably 70-100 g / L. The content of calcium sulfate in high-calcium brine is preferably 0.5-1.5 g / L, more preferably 0.4-1.0 g / L, and most preferably 0.2-0.5 g / L. The mixing ratio of ammonia-alkali waste liquid and water is ammonia-alkali waste liquid:water (volume)=1:0.1-2, preferably 1:0.1-1, more preferably 1:0.1-0.5, most preferably 1:0.2. . The high-calcium brine is preheated to 50°C by heat exchange with secondary steam (primary preheating) and / or condensed water (secondary preheating) re...
Embodiment 1
[0067]1. Ammonia-alkali waste liquid and water are blended according to the volume ratio of ammonia-alkali waste liquid: water=1:0.2 and injected into sodium sulfate type salt mine for underground desulfurization. The production calcium chloride content is 60g / L and the magnesium content is 0g / L L. Calcium sulfate content 1.2g / L, high calcium brine saturated with sodium chloride, after heat exchange with secondary steam (first-level preheating) and condensed water (secondary preheating) through the pump (high-calcium brine temperature rise to about 50°C) into the four-effect brine concentration system (multi-effect forced circulation evaporator) through the feeding pump, and the concentrated suspension is sent to the cyclone for solid-liquid separation through the salt slurry pump, and the bottom flow returns to the raw brine tank. The top flow enters the first-stage MVR evaporation salt production process through the pump, the salt slurry evaporated and concentrated by the fir...
Embodiment 2
[0077] 1. Ammonia-alkali waste liquid and water are blended according to the volume ratio of ammonia-alkali waste liquid: water=1:0.1 and injected into sodium sulfate type salt mine for underground desulfurization, producing calcium chloride content of 80g / L and magnesium content of 0g / L L. High-calcium brine with a calcium sulfate content of 0.6g / L and saturated with sodium chloride is pumped through the pump to exchange heat with secondary steam (first-stage preheating) and condensed water (secondary preheating), and then pumped into the Four-effect brine concentration system, the concentrated suspension is transported to the cyclone by the salt slurry pump for solid-liquid separation, the bottom flow is returned to the raw brine tank, the top flow is pumped into the first-stage MVR evaporation salt production process, and the first-stage MVR The salt slurry concentrated by salt evaporation is separated from solid and liquid by a cyclone, and the underflow salt slurry is then...
PUM
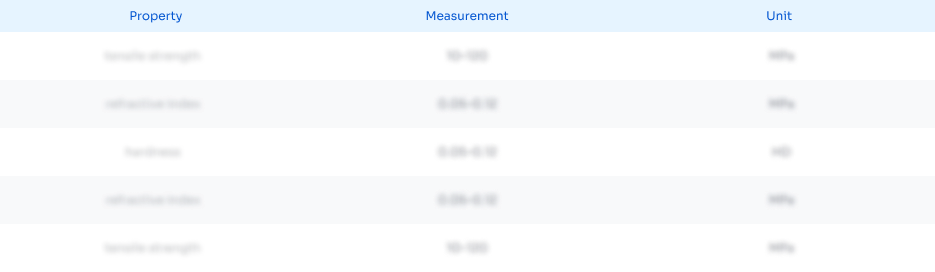
Abstract
Description
Claims
Application Information

- Generate Ideas
- Intellectual Property
- Life Sciences
- Materials
- Tech Scout
- Unparalleled Data Quality
- Higher Quality Content
- 60% Fewer Hallucinations
Browse by: Latest US Patents, China's latest patents, Technical Efficacy Thesaurus, Application Domain, Technology Topic, Popular Technical Reports.
© 2025 PatSnap. All rights reserved.Legal|Privacy policy|Modern Slavery Act Transparency Statement|Sitemap|About US| Contact US: help@patsnap.com