Aclinal self-upsetting, stirring and friction welding method and tool
A technology of friction stir welding and welding method, applied in welding equipment, manufacturing tools, non-electric welding equipment, etc., can solve problems such as low precision, welding defects, and reduced work efficiency
- Summary
- Abstract
- Description
- Claims
- Application Information
AI Technical Summary
Problems solved by technology
Method used
Image
Examples
Embodiment Construction
[0025] The technical solution of the present invention will be further described below in conjunction with the accompanying drawings.
[0026] refer to figure 1 , a non-inclined self-upsetting friction stir welding welding method, comprising the following steps,
[0027] Step 1. Fix the material to be welded on the workbench, and form a weld bead 2 at the welding place of two pieces of material to be welded 1, and the thickness of the material to be welded is 3 to 100mm;
[0028] Step 2, the stirring head 3 is placed above the welding surface of the material to be welded, where the stirring head can be placed at any position above the welding surface, at this time, the axial direction of the stirring head coincides with the normal direction of the material to be welded;
[0029] Step 3, the stirring head starts to rotate under the action of the rotating mechanism and the lifting mechanism and falls in place. The rotating mechanism that drives the stirring head to rotate and t...
PUM
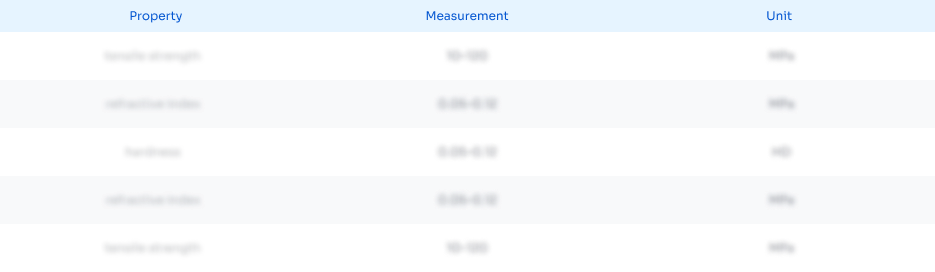
Abstract
Description
Claims
Application Information

- R&D
- Intellectual Property
- Life Sciences
- Materials
- Tech Scout
- Unparalleled Data Quality
- Higher Quality Content
- 60% Fewer Hallucinations
Browse by: Latest US Patents, China's latest patents, Technical Efficacy Thesaurus, Application Domain, Technology Topic, Popular Technical Reports.
© 2025 PatSnap. All rights reserved.Legal|Privacy policy|Modern Slavery Act Transparency Statement|Sitemap|About US| Contact US: help@patsnap.com