A kind of magnesium alloy melt refining method
A magnesium alloy and melt technology, applied in the field of magnesium alloy melt refining, can solve the problems of large flux amount, large bubble size, uneven distribution, etc. The effect of efficiency
- Summary
- Abstract
- Description
- Claims
- Application Information
AI Technical Summary
Problems solved by technology
Method used
Image
Examples
Embodiment 1
[0035] Put 5kg of ordinary commercially purchased AZ91 magnesium alloy into the heat preservation container for melting, and after melting, keep it at 678°C for 8 minutes (conventional treatment method); Insert the hollow tool head of the inert gas into the magnesium alloy melt in the heat preservation container; start the flux quantitative supply system after adjusting the gas flow and pressure, and quickly adjust the flux quantitative setting control device; start the high-intensity sound cavitation system, set the sound Cavitation frequency and power, the system modulates the resonance state to process the alloy melt for a period of time; after the treatment of the magnesium alloy melt, first turn off the high-intensity acoustic cavitation system and then turn off the flux quantitative supply system, and then quickly insert the magnesium alloy into the melt The hollow tool head is removed and finally the inert gas supply system is turned off.
[0036]The relevant parameters...
Embodiment 2
[0039] Put 10kg of ordinary commercially purchased AZ91 magnesium alloy into the heat preservation container for melting, and after melting, keep it at 693°C for 15 minutes (conventional treatment method); Insert the hollow tool head of the inert gas into the magnesium alloy melt in the heat preservation container; start the flux quantitative supply system after adjusting the gas flow and pressure, and quickly adjust the flux quantitative setting control device; start the high-intensity sound cavitation system, set the sound Cavitation frequency and power, the system modulates the resonance state to process the alloy melt for a period of time; after the treatment of the magnesium alloy melt, first turn off the high-intensity acoustic cavitation system and then turn off the flux quantitative supply system, and then quickly insert the magnesium alloy into the melt The hollow tool head is removed and finally the inert gas supply system is turned off.
[0040] The relevant paramet...
Embodiment 3
[0043] Put 20kg of ordinary commercially purchased AZ80 magnesium alloy into the heat preservation container for melting, and after melting, keep it at 687°C for 15 minutes (conventional treatment method); Insert the hollow tool head of the inert gas into the magnesium alloy melt in the heat preservation container; start the flux quantitative supply system after adjusting the gas flow and pressure, and quickly adjust the flux quantitative setting control device; start the high-intensity sound cavitation system, set the sound Cavitation frequency and power, the system modulates the resonance state to process the alloy melt for a period of time; after the treatment of the magnesium alloy melt, first turn off the high-intensity acoustic cavitation system and then turn off the flux quantitative supply system, and then quickly insert the magnesium alloy into the melt The hollow tool head is removed and finally the inert gas supply system is turned off.
[0044] The relevant paramet...
PUM
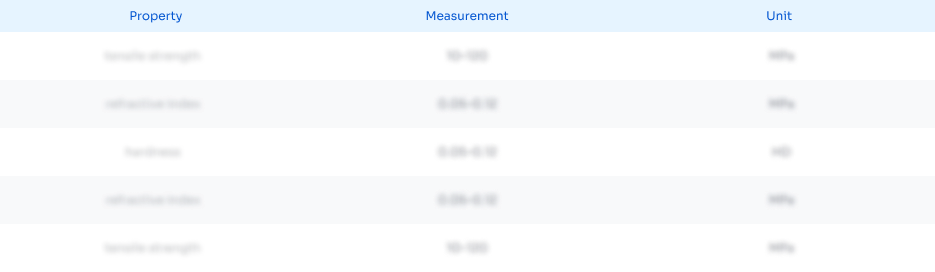
Abstract
Description
Claims
Application Information

- Generate Ideas
- Intellectual Property
- Life Sciences
- Materials
- Tech Scout
- Unparalleled Data Quality
- Higher Quality Content
- 60% Fewer Hallucinations
Browse by: Latest US Patents, China's latest patents, Technical Efficacy Thesaurus, Application Domain, Technology Topic, Popular Technical Reports.
© 2025 PatSnap. All rights reserved.Legal|Privacy policy|Modern Slavery Act Transparency Statement|Sitemap|About US| Contact US: help@patsnap.com