Semi-solid rheological squeeze casting forming method of flame retardant magnesium alloy
A semi-solid rheological and squeeze casting technology, which is applied in the field of semi-solid rheological squeeze casting of flame-retardant magnesium alloys, can solve the problem of difficulty in obtaining parts with complete shapes, increased viscosity of magnesium alloy melt, and influence on the mechanical properties of alloys and other problems, to achieve the effect of strong practicability of the process, reduction of oxidation loss, and improvement of utilization rate
- Summary
- Abstract
- Description
- Claims
- Application Information
AI Technical Summary
Problems solved by technology
Method used
Image
Examples
Embodiment 1
[0033] This embodiment relates to a flame-retardant magnesium alloy obtained by adding metal Ca to an AZ91 alloy ingot, wherein the mass fraction of Ca is 1.5%.
[0034] The preparation method of the fire-resistant magnesium alloy includes three process steps of smelting, preparation of semi-solid slurry and subsequent extrusion casting.
[0035] Among them, the previous smelting process is in SF6 and CO 2 Under the condition of mixed gas protection, the specific steps are: put the dried AZ91 alloy ingot into the SF 6 / CO 2 Melt in a gas-protected crucible resistance furnace, add Ca at 700°C after the alloy is melted, refine and remove slag at 730°C, and cool the melt down to 610-630°C.
[0036] The subsequent semi-solid slurry preparation process is: use a quantitative scoop to extract the magnesium alloy liquid at 610-630°C, then put the blowing device into the magnesium alloy liquid for blowing and stirring, and prepare it into a semi-solid slurry. Among them, the air bu...
Embodiment 2
[0040] This embodiment relates to a flame-retardant magnesium alloy obtained by adding metal Ca to an AM50 alloy ingot, wherein the mass fraction of Ca is 3.0%.
[0041] The preparation method of the fire-resistant magnesium alloy includes three process steps of smelting, preparation of semi-solid slurry and subsequent extrusion casting.
[0042] Among them, the previous smelting process is in SF 6 and CO 2 Under the condition of mixed gas protection, the specific steps are: put the dried AM50 alloy ingot into SF 6 / CO 2 Melt in a gas-protected crucible resistance furnace, add Ca at 700°C after the alloy is melted, refine and remove slag at 730°C, and cool the melt down to 610-630°C. The subsequent semi-solid slurry preparation process is: use a quantitative scoop to extract the magnesium alloy liquid at 610-630°C, then put the blowing device into the magnesium alloy liquid for blowing and stirring, and prepare it into a semi-solid slurry. Among them, the air bubble flow r...
PUM
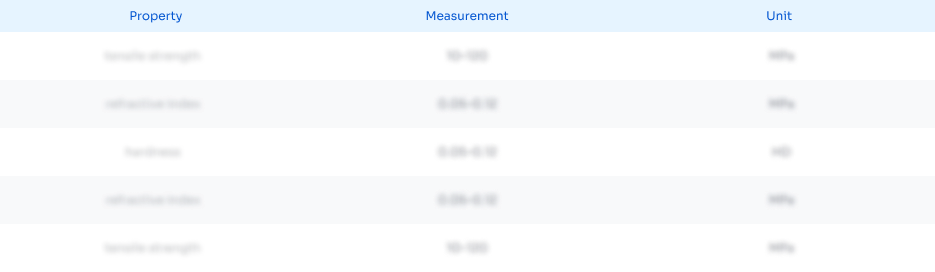
Abstract
Description
Claims
Application Information

- R&D
- Intellectual Property
- Life Sciences
- Materials
- Tech Scout
- Unparalleled Data Quality
- Higher Quality Content
- 60% Fewer Hallucinations
Browse by: Latest US Patents, China's latest patents, Technical Efficacy Thesaurus, Application Domain, Technology Topic, Popular Technical Reports.
© 2025 PatSnap. All rights reserved.Legal|Privacy policy|Modern Slavery Act Transparency Statement|Sitemap|About US| Contact US: help@patsnap.com