Method for preparing micro-nano textures through ultrasonic vibration
An ultrasonic vibration, micro-nano technology, applied in the manufacture of micro-structure devices, micro-structure technology, micro-structure devices, etc., can solve the problem that mask lithography cannot achieve size control, scanning probe processing efficiency is low, and equipment is expensive. Surface and other problems, to achieve the effect of reducing the time for making masks, less stress, and better surface quality
- Summary
- Abstract
- Description
- Claims
- Application Information
AI Technical Summary
Problems solved by technology
Method used
Image
Examples
Embodiment 1
[0024] Embodiment 1: In this method, firstly, a layer of photoresist is evenly coated on the surface of the substrate by using a coater; the substrate with photoresist is subjected to interference exposure in a laser interference system to realize texturing of the photoresist processing; finally, the substrate is placed in an ultrasonic processing system for processing, and the substrate material in the non-photoresist-covered area will be removed. As the ultrasonic processing time increases, the removal depth will gradually increase. By controlling the exposure of laser interference lithography parameters and ultrasonic vibration processing parameters to achieve size-controllable and large-area periodic micro-nano texture preparation.
[0025] The preparation method of the micro-nano texture in the present invention adopts the processing method of laser interference photolithography and ultrasonic vibration.
[0026] Process flow of the present invention is:
[0027] First, ...
PUM
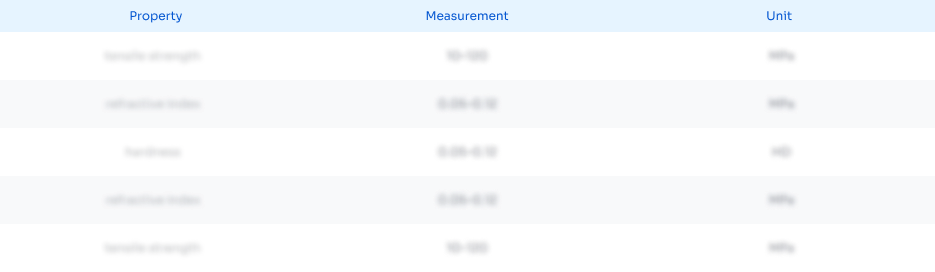
Abstract
Description
Claims
Application Information

- R&D
- Intellectual Property
- Life Sciences
- Materials
- Tech Scout
- Unparalleled Data Quality
- Higher Quality Content
- 60% Fewer Hallucinations
Browse by: Latest US Patents, China's latest patents, Technical Efficacy Thesaurus, Application Domain, Technology Topic, Popular Technical Reports.
© 2025 PatSnap. All rights reserved.Legal|Privacy policy|Modern Slavery Act Transparency Statement|Sitemap|About US| Contact US: help@patsnap.com