A method for preparing unburned bricks or blocks by extracting alumina by-products from fly ash
A technology of fly ash and alumina, applied in cement production and other directions, can solve problems such as no application, and achieve the effects of low price, lower production cost, and enhanced strength
- Summary
- Abstract
- Description
- Claims
- Application Information
AI Technical Summary
Problems solved by technology
Method used
Image
Examples
Embodiment 1
[0019] The invention provides a method for preparing unburned bricks or blocks by extracting alumina by-products from fly ash, comprising:
[0020] Step 1. Pretreatment of raw materials: Grinding silicon-calcium slag, desulfurized gypsum and quicklime respectively to form a powder of ≤180 mesh for future use. Among them, silicon-calcium slag is alumina clinker produced by calcining fly ash and limestone ingredients Solid waste produced after mixing with lye;
[0021] Step 2, first transport 45Kg of silicon-calcium slag, 25Kg of fly ash and 5Kg of desulfurized gypsum to the mixer for mixing and stirring in parts by weight. The stirring time is 5 minutes, and the stirring speed is 150 rpm. While stirring, 13Kg of quicklime and 30Kg of river sand, after stirring evenly, add 5Kg of cement to mix and stir for 3 minutes, and finally add 25Kg of water to stir for 15 minutes, the cement is Portland cement;
[0022] Step 3, forming: transport the mixed material evenly stirred in step ...
Embodiment 2
[0028] The invention provides a method for preparing unburned bricks or blocks by extracting alumina by-products from fly ash, comprising:
[0029] Step 1. Pretreatment of raw materials: Grinding silicon-calcium slag, desulfurized gypsum and quicklime respectively to form a powder of ≤180 mesh for future use. Among them, silicon-calcium slag is alumina clinker produced by calcining fly ash and limestone ingredients Solid waste produced after mixing with lye;
[0030] Step 2, first transport 35Kg of silicon-calcium slag, 15Kg of fly ash and 3Kg of desulfurized gypsum to the mixer for mixing and stirring, the stirring time is 1 minute, and the stirring speed is 130 rpm, while stirring, add 8Kg of quicklime and 15Kg of river sand, after stirring evenly, add 1Kg of cement for mixing and stirring for 1-3 minutes, and finally add 20Kg of water for stirring for 5 minutes, the cement is sulphoaluminate cement;
[0031] Step 3, forming: transport the mixed material evenly stirred in s...
Embodiment 3
[0037] The invention provides a method for preparing unburned bricks or blocks by extracting alumina by-products from fly ash, comprising:
[0038] Step 1. Pretreatment of raw materials: Grinding calcium silicate slag, desulfurized gypsum and quicklime respectively to form a powder of ≤180 mesh for future use, wherein calcium silicate slag is alumina clinker produced by calcining fly ash and limestone ingredients Solid waste produced after mixing with lye;
[0039] Step 2, first transport 40Kg of silicon-calcium slag, 20Kg of fly ash and 4Kg of desulfurized gypsum to the mixer for mixing and stirring in parts by weight. The stirring time is 3 minutes, and the stirring speed is 140 rpm. While stirring, 10Kg of quicklime and 22Kg of river sand, after stirring evenly, add 3Kg of cement and mix and stir for 2 minutes, and finally add 22Kg of water and stir for 10 minutes, and the cement is glass fiber reinforced cement;
[0040]Step 3, molding: transport the mixed material evenly...
PUM
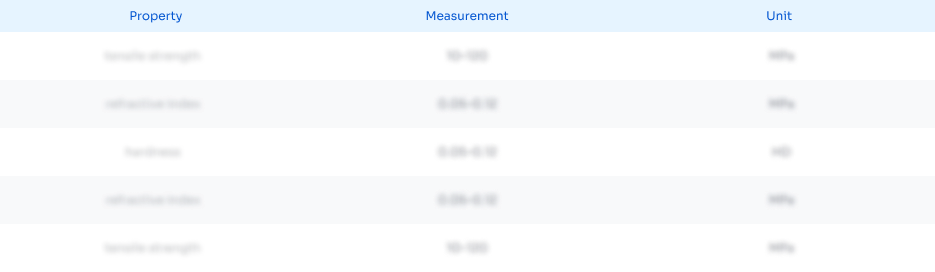
Abstract
Description
Claims
Application Information

- R&D Engineer
- R&D Manager
- IP Professional
- Industry Leading Data Capabilities
- Powerful AI technology
- Patent DNA Extraction
Browse by: Latest US Patents, China's latest patents, Technical Efficacy Thesaurus, Application Domain, Technology Topic, Popular Technical Reports.
© 2024 PatSnap. All rights reserved.Legal|Privacy policy|Modern Slavery Act Transparency Statement|Sitemap|About US| Contact US: help@patsnap.com