Bifunctional catalyst for heavy oil cracking and coke gasification, and preparation method thereof
A dual-function catalyst and catalyst technology, applied in the direction of physical/chemical process catalysts, molecular sieve catalysts, chemical instruments and methods, etc., can solve the problems of insufficient effective gas yield, low catalytic activity, low conversion rate of heavy oil, etc., and achieve good resistance Sulfur nitrogen, increase hydrogen content, increase the effect of conversion rate
- Summary
- Abstract
- Description
- Claims
- Application Information
AI Technical Summary
Problems solved by technology
Method used
Image
Examples
Embodiment 1
[0047] The preparation method of the catalyst: Dissolve 10g of aluminum sulfate in 30mL of water, add sodium hydroxide solution to adjust the pH value to prepare aluminum sol; add a mixture of Y-type molecular sieve and macroporous alumina, the mass ratio is 1:1, and stir for 1 hour, wherein The content of molecular sieve in the catalyst is 40%, and the content of macroporous alumina in the catalyst is 40%. A certain amount of concentrated hydrochloric acid (36%) is added, and the mass ratio of hydrochloric acid to the total aluminum of the catalyst (calculated as alumina) is 15 :100, stirred for 30 minutes, added 20mL of 5mol / L magnesium chloride solution, continued to stir for 30 minutes, sprayed, dried at 120°C for 6h, and roasted at 550°C for 4h to obtain the required catalyst.
[0048] test:
[0049] The heavy oil required for the experiment was evaluated, and the evaluation data are shown in Table 1.
[0050] Table 1 Residual oil physical property characterization data ...
Embodiment 2
[0062] Dissolve 10g of sodium metaaluminate in 30mL of water, add sodium hydroxide solution to adjust the pH value to prepare aluminum sol; add a mixture of X-type molecular sieve and macroporous alumina, the mass ratio is 1:3, and stir for 2 hours; add a certain amount of Concentrated nitric acid (36%), the mass ratio of nitric acid to catalyst total aluminum (calculated as alumina) is 2:100, stir for 50 minutes, add 3mol / L calcium nitrate solution, continue stirring for 30 minutes, spray molding, and dry at 120°C Calcined for 6 hours at 580° C. for 4 hours to obtain the desired catalyst, in which the X-type molecular sieve content is 2 wt%, and the calcium element (calculated as calcium oxide) content is 2 wt%.
[0063] The method described in Example 1 was used to test the catalyst obtained in Example 2. The cracking test results are shown in Table 4. Gasification test results: the reaction temperature is 900°C, the reaction time is 40 minutes, the gasification agent is wa...
Embodiment 3
[0067] Adopt the aluminum sol of embodiment 1; Add the mixture of A-type molecular sieve and macroporous alumina, mass ratio 1:5, stir 1.5 hours; Add a certain amount of concentrated carbonic acid (40%), carbonic acid and catalyst total aluminum (with alumina The mass ratio is 25:100, stirred for 60 minutes, added 3mol / L potassium carbonate solution, continued to stir for 30 minutes, sprayed, dried at 120°C for 6 hours, and calcined at 540°C for 4 hours to obtain the desired catalyst. The content of type A molecular sieve in the medium is 45wt%, the content of gasification active components (calculated as potassium oxide and calcium oxide) is 40wt%, and the molar ratio of potassium and calcium elements in the gasification active components is 1:1.
[0068] The catalyst obtained in Example 3 was tested by the method described in Example 1. The cracking test results are shown in Table 5. Gasification test results: reaction temperature 900°C, reaction time 40 minutes, gasificati...
PUM
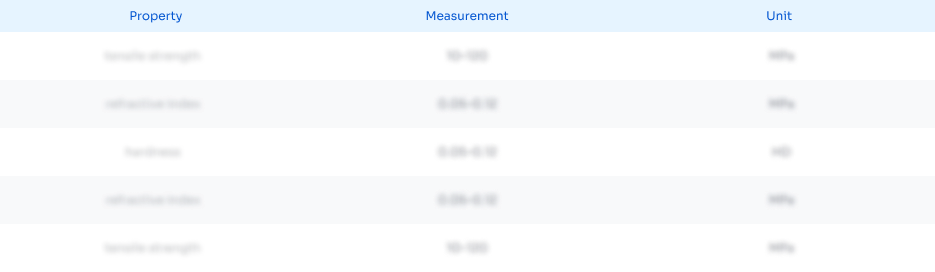
Abstract
Description
Claims
Application Information

- Generate Ideas
- Intellectual Property
- Life Sciences
- Materials
- Tech Scout
- Unparalleled Data Quality
- Higher Quality Content
- 60% Fewer Hallucinations
Browse by: Latest US Patents, China's latest patents, Technical Efficacy Thesaurus, Application Domain, Technology Topic, Popular Technical Reports.
© 2025 PatSnap. All rights reserved.Legal|Privacy policy|Modern Slavery Act Transparency Statement|Sitemap|About US| Contact US: help@patsnap.com